Synopsis: Picking the right polyurethane can be a bewildering task. In this article, Otto Heuer explains how to distinguish differences among what’s on the shelves and how it’s made to help you better identify the finish you need. The type of oil used in the manufacturing process is a good guide to several aspects of finish quality, and Heuer offers direction on which finishes will cloud or darken over time. He talks about how to gauge hardness and adhesion and how to apply polyurethane. He shares tips on safety and how to avoid bubbles in your resulting finish. A side article by Nancy Lindquist discusses spraying polyurethanes and other varnishes.
Companies manufacturing polyurethane describe it as a stunning finish that is unbelievably tough. Even though some craftsmen complain that the glossy finish has an artificial, plastic look, it does wear well, resists scratches and other abrasions, and is virtually impervious to household chemicals and detergents, alcohol, even boiling water.
Picking the right polyurethane for your job can be a bewildering journey through a maze of cans: Urethane Finish; Polyurethane Varnish; Clear Gloss Urethane; Spar Urethane; Polyurethane Liquid Plastic; Polyurethane Reinforced Varnish; Spar Urethane Varnish. The composition labels on the cans are difficult to understand, and at times, remind me of the old saying about well-organized confusion. I know one man who was so confused he wasn’t sure if he bought polyurethane or something being compared to polyurethane (he bought oil-based varnish).
Part of the confusion comes from the chemical complexity of polyurethanes. They are not merely blends of solvents and resins, but highly reacted chemical compounds. In contrast, lacquers are relatively simple mixtures of nitrocellulose (as a film-former), hard resins (to increase gloss), and plasticizers (to make the film more flexible). Traditional varnishes, mixtures of vegetable oils and natural or synthetic resins, are slightly more complex than lacquers. The varnish is heated during the manufacturing process, promoting chemical reactions among the components.
Because of the elaborate equipment needed to produce the complex polyurethane, many small- to medium-size finishing companies don’t even manufacture it, They buy “concentrated” resins from some of the country’s major chemical companies, blend it with their own ingredients, and market it under their own names. This may explain why I found so many similarities among various brands. I tested 15 clear gloss and 12 satin luster polyurethanes on wood and glass panels as I researched this article. The finishes were so consistently clear and strong I concluded that most of the differences in quality of finish had to do with application methods. Price is also an important factor. If you buy a brand-name product, you improve your chances of getting a good finish. If you buy a bargain-basement brand that’s considerably cheaper than the brandname ones, you’re tilting the odds in favor of an inferior result.
The terms polyurethane and urethane have nothing to do with quality—both terms, along with names like urethane polymer and isocyanate polymer, refer to the same type of finish. The name game seems to be mostly a sales gimmick—a label advertising isocyanate polymer might scare people away. “Plastic” is another sales pitch. Although polyurethanes are chemically similar to plastics, the term “synthetic” would be more correct in describing polyurethane, epoxy, and other modern finishes.
From Fine Woodworking #59
For the full article, download the PDF below:
Fine Woodworking Recommended Products
Dividers
Compass
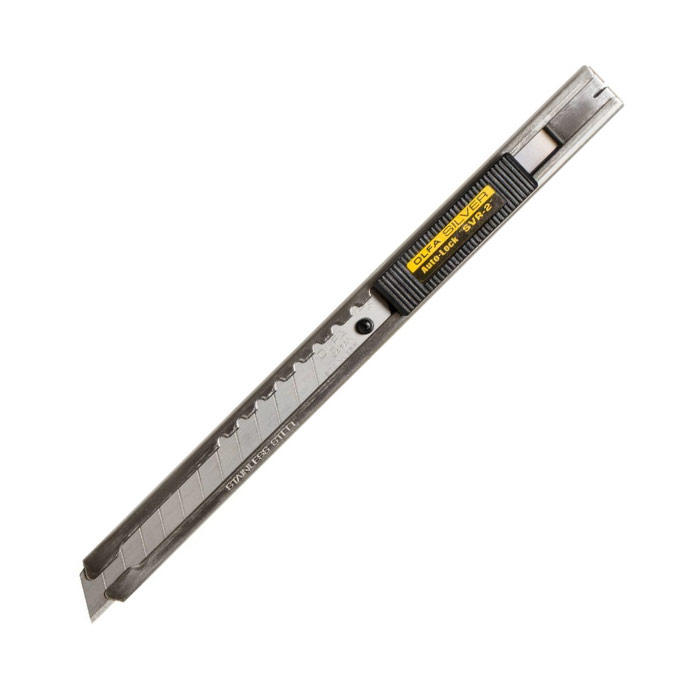
Olfa Knife
Log in or create an account to post a comment.
Sign up Log in