Synopsis: Ronald Layport was granted visitation rights, of a sort, by the client who bought his open hutch. It was a labor of love. The piece is based on cupboards built between 1730 and 1840 and uses joinery common to the period, such as pinned mortise-and-tenon, frame-and-panel, and dovetailed solid-board construction. Layport cut tenons on the tablesaw and hand-chopped all 96 mortises with a chisel (he suggests that others use a router). He explains how he arrived at the design, how to build and detail the lower and carcases. Detailed project plans accompany the article, along with a list of material dimensions. There’s also information on molding profiles.
Since this curly maple hutch was my first commissioned piece, I had mixed feelings about parting with it, Although I’ve been designing and building furniture for myself and family members for about six years, I was uncomfortable with the thought that I might never see this piece again. However, I’m pleased to report that the “letting go” turned out to be a joy rather than a problem. The couple who commissioned the hutch was every bit as delighted with it as I was exhausted upon its completion. I was even granted “Visitation rights.”
The open hutch shown here is similar to cupboards that were common in middle America between 1730 and 1840. These pieces were sometimes called hutch cupboards, open hutches, sideboards with hutch tops, and even dressers, and their designs and styles were as varied as the terms used to describe them. I used joinery common to the period, such as pinned mortise-and-tenon, frame-and-panel and dovetailed solid-board construction. I cut tenons on the tablesaw and hand-chopped mortises with a chisel, although I admit that a router is an appealing alternative for cutting the 96 mortises in this hutch. I always hand-cut dovetails because I enjoy the process, and I like seeing perfectly pointed pins running down the corner of a drawer. To create a dimensional effect, I edged the stiles, drawers, shelves and back boards with more than 200 ft. of hand-tooled bead. A wood shaper or router would make short work of forming this bead, but the techniques that I discuss for using a scratch stock provide a lot of satisfaction and an unmistakable hand-crafted quality.
Although I used hand tools to achieve a desired effect, I am not a fanatic on this issue. I could never have built this piece without my jointer, thickness planer, tablesaw and drill press. My power tools handled the bulk of the work and left me with energy for hand-working the details.
Curly maple is sometimes called tiger maple due to its cross-grain stripe. This highly figured wood is said to be found in only one out of every 10,000 maple trees. In fact, I waited a year and a half for this tree to be harvested by sawyers in northeastern Ohio. The hutch could be equally spectacular in walnut or cherry with a simple hand-rubbed carnauba wax finish.
From Fine Woodworking #89
For the full article, download the PDF below:
Fine Woodworking Recommended Products
Drafting Tools
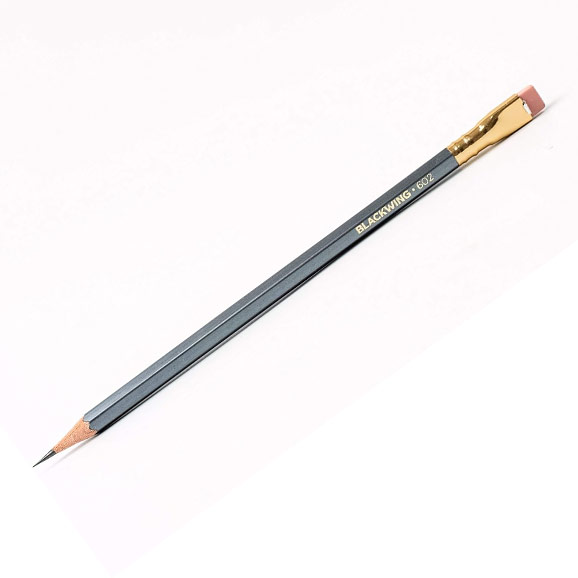
Blackwing Pencils
Log in or create an account to post a comment.
Sign up Log in