Templates Guide the Way
Create elegant curves and furniture parts with router templatesSynopsis: Professional furniture maker Doug Peterman details his fail-proof approach to shaping wood with router templates. Get step-by-step instruction on shaping templates with sanders, securing the template to a workpiece, and routing a workpiece with bearing-guided router bits. In addition to telling you the right way to rout with a template, Peterman gives troubleshooting tips to prevent bumps, dips, burns, and tearout with a router.
From Fine Woodworking #170
When the talk turned to tools at a recent woodworkers’ meeting, I surprised myself by naming router templates as my favorite. Don’t get me wrong: I love hand tools and use them constantly, but my work would be less efficient and less profitable without these simple but versatile templates.
Router templates can be used to create and fine-tune furniture forms before cutting into expensive stock. They allow me to see a design full-size and in relation to the other parts of a piece. Not to mention, templates make it easy to reproduce identical parts.
Almost all template-routing operations require only a handful of tools, including a router, two common bearing-guided bits, a bandsaw, a sander, and a shopmade template. With those items and a few drawing tools, such as a compass or even french curves, you are fully equipped to tackle any template-routing job.
Templates can be made from any stiff sheet material with enough strength and thickness to guide the bearing on a router bit. In a pinch I’ve even used scrap wall paneling and old crate lumber, but there are better choices. Mainly, I use two materials: 1⁄8-in.-thick Masonite for one-offs and 1⁄4-in.-thick Baltic-birch plywood for production. Both have the basic characteristics of dimensional stability and consistency (no hard or soft spots), and are readily available.
Trusting your eye is the quickest route to getting the shape you want in a template, but drawing tools will help you get there.
I usually begin by sketching the template pattern directly on the surface of the workpiece, especially when I’m working to preserve the grain in a particular board. Once I’m satisfied with the shape, I transfer it to the template stock.
When drawing the pattern on the template, it’s a good idea to add at least 1 in. of material lead-in and exit beyond the workpiece edge wherever possible. Without it, the bit can catch as you try to make the first corner of the template meet the bearing. Believe me, I’ve done it.
Whether you draw a pattern freehand or with drawing tools, you often will be left with bumpy lines and rough transitions that need to be smoothed out. The trick to achieving a smooth, or fair, curve is to get your eyes right down near the drawing surface and look along the line. Bumps and dips are easy to see, but also look for transitions that are too abrupt. Work your way along the line, refining it until the curves are fair.
For the full article, download the PDF below.
Fine Woodworking Recommended Products
Ridgid EB4424 Oscillating Spindle/Belt Sander
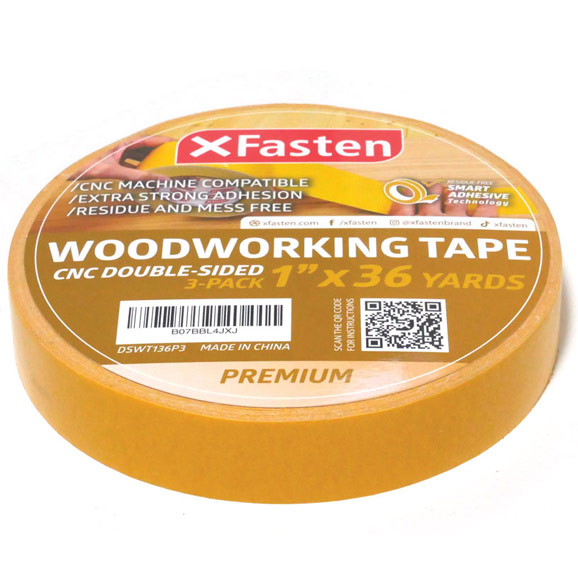
Double Sided Tape
Veritas Wheel Marking Gauge
Log in or create an account to post a comment.
Sign up Log in