Preventing Tear-Out
The problem of excessive tear-out at the bottom of drill-press holes can be solved with a simple metal collar. I discovered the collar solution during a 30-unit production run of a small piece of furniture. Each unit required a drilling operation of eighteen holes in warped 1×12 pine. Without question, the tear-out problems I experienced were because the warped stock was inadequately supported on the drill table.
I’m aware that the classic prevention for tear-out is to support the stock to be drilled with a scrap back-up board. This I wished to avoid because of the hazard, nuisance and expense. I used my small metal lathe to turn a substitute for the backup board a steel collar with a 1/32-in. protruding lip to compress and support the wood in the area of the hole. When the wood is adequately supported and compressed in advance of the rotating bit, the result is a clean hole.
The profile of the collar is shown in the sketch. Except for matching the collar’s bore to the drill bit used, the dimensions are arbitrary. Turn the bottom of the collar flat (perhaps even a shade concave) to prevent the collar from rocking.
To install the collar on the drill press, put double-sided tape on the bottom of the collar and slip it over the drill bit. With the bit lowered into the table, carefully slide the collar down and press it onto the table. Counterboring the hole in the table will prevent shavings from jamming the collar hole.
Carl Hogberg, North Chatham, Mass.
Fine Woodworking Magazine, August 1980 No. 23
Fine Woodworking Recommended Products
Grizzly G0495X Industrial Helical Cutterhead 8-in. Jointer
JessEm Mite-R Excel II Miter Gauge
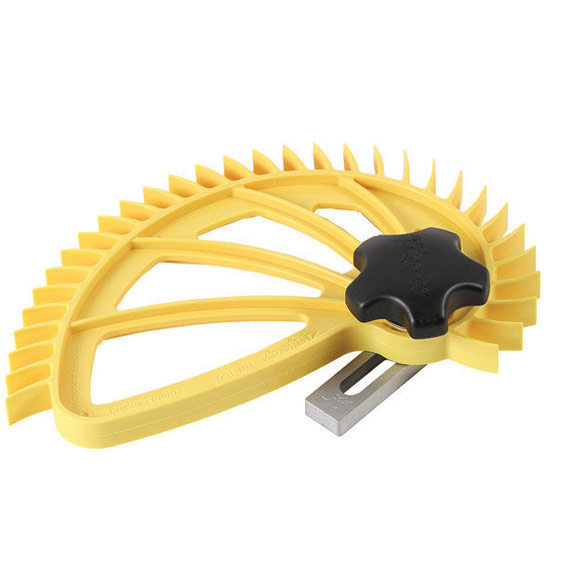
Hedgehog featherboards
Log in or create an account to post a comment.
Sign up Log in