Using Hand Screws
Time-honored tool is still first choice for a variety of shop tasksSynopsis: Hand screws may have been around since ancient times, but that doesn’t make them outdated or obsolete. In fact, they have lasted precisely because they can do a variety of tasks better than anything that has come along since. They are adept at holding a workpiece for glue-up, especially when it involves angled shapes, edge repairs, and delicate work. They’re invaluable for keeping edges aligned during panel glue-ups. They easily hold small workpieces securely at the bench when your vise is too big or too clumsy. In fact, Garrett Hack uses hand screws for so many jobs around the shop that he wouldn’t be without them.
Useful tools survive. They find a place in your shop because they do certain tasks easily or well. With all sorts of modern clamps available, simple hand screws might seem outdated—quaint reminders of woodworking past. Hardly. Their design is ancient, but hand screws are still my first choice for a variety of tasks. Their parallel screws let them grip where other clamps won’t, and their large, flat jaws can act as built-in cauls. This lets them fill several roles in glue-ups and in securing small or oddly shaped work.
The hand screw’s basic design—a pair EASY AS RIDING A BIKE of wooden jaws linked with two threaded handles that screw the jaws open or closed —probably came from the Romans. Modern versions feature steel screws threaded into nuts embedded in the jaws. On most, these embedded nuts also can rotate, allowing the jaws to be angled considerably for grabbing tapered work.
Hand screws are commonly available with jaws from 4 in. to 12 in. long. The reach—and the opening—of the jaws is usually half of the length. Hand screws can be frustrating to use at first. They seem to adjust slowly, and it’s easy to get confused and find yourself opening one handle while closing another.
The trick is to grab both handles and pedal the jaws (just as you would a bicycle) open or closed to an approximate fit of what you are clamping. Place the clamp in position, and then close up the jaws by tightening both handles. It takes a bit of practice to know which handle to turn to fine-tune the angle of the jaws, but you’ll soon get the hang of it.
A highly adaptable clamp
When gluing up panels, the stout and rigid jaws of a hand screw are particularly useful for keeping the boards flat and flush with one another. As you bring the boards together with bar or pipe clamps, it’s common for the panel to bow slightly, especially if the stock is thin. I use a hand screw between the bowed face and the side of one of the bar clamps to pinch the panel flat, adjusting the clamp one-handed if I have to. Other clamps are much harder to use for this purpose, as it is difficult to get a grip on a round pipe clamp or the thin edge of a bar clamp.
Another common problem assembling a panel is slight misalignment of the faces of the boards.
From Fine Woodworking #194
Fine Woodworking Recommended Products
Veritas Wheel Marking Gauge
Tite-Mark Marking Gauge
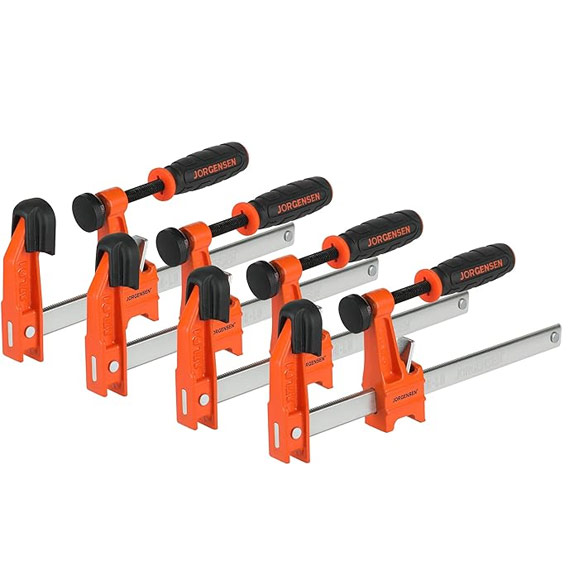
Jorgensen 6 inch Bar Clamp Set, 4 Pack
Comments
Excellent article with a lot of good information. I find myself using these clamps often and with good results. I learned a couple new tricks for clamping as well.
Log in or create an account to post a comment.
Sign up Log in