STL170: Biscuit Joiner vs. Dowel Jigs
John Tetreault joins Mike and Ben as they answer questions about dowel jigs, biscuit joiners, tricky glue ups, dust collection and their all-time favorite tools of all timeThis episode of is sponsored by Varathane:
From furniture and cabinets to floors and crafts, professionals and DIYers alike have trusted the ultimate color and protection of Varathane since 1958. Varathane Wood Stain gives rich, true color in one coat. And Varathane Triple Thick Polyurethane has the durability of three coats in one. Visit varathanemasters.com for details.
If you have questions you’d like us to answer on the show, send them in to shoptalk@taunton.com. You can also use the voice memo app on your phone and email us a 30 second audio recording, or if you’re old-school you can leave a voicemail by calling 203-304-3456.
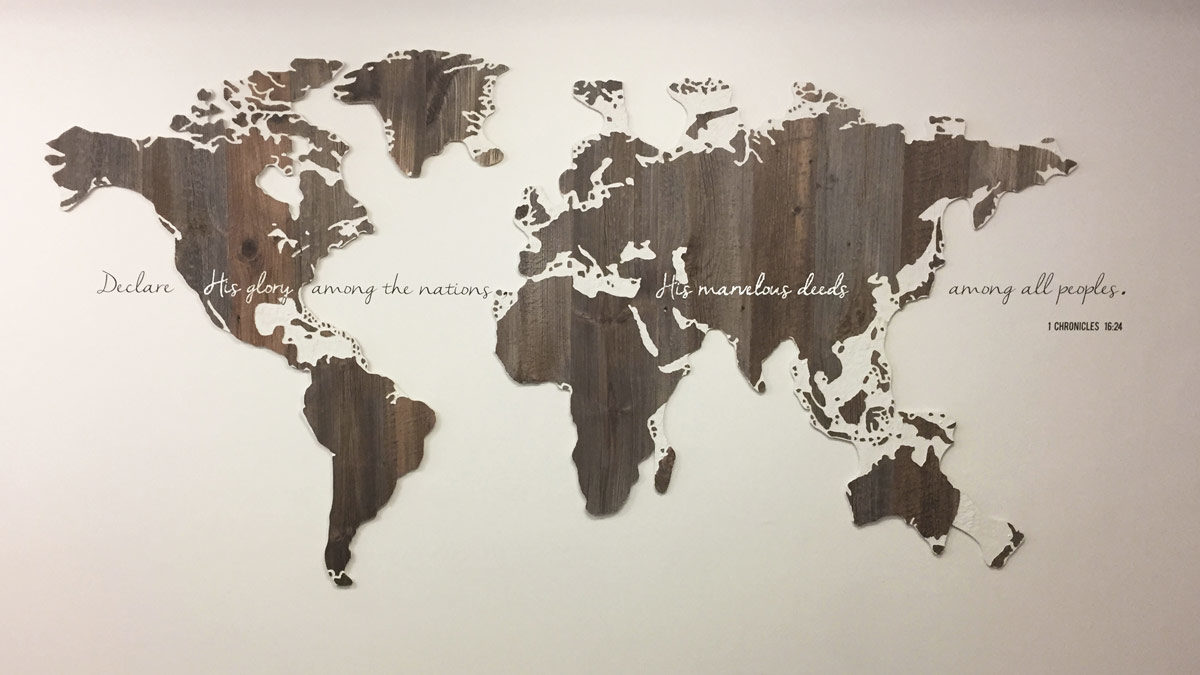
Question 1:
Recently, I’ve seen a lot of arts and craft projects assembled with biscuits. I don’t have a biscuit joiner, and given the $200 price tag, I’m wondering if I’d be better off going with a high-quality dowel jig. Clearly, the speed of adjustment favors the biscuit joiner. I would very much like a domino, but I don’t think that’s in the budget, especially after a recent table saw upgrade. -Tom
- Video: Accurate Biscuit Joints by Tony O’Malley #165–Sept/Oct 2003 Issue
- Fine Furniture with Biscuit Joints by Michael Fortune #227–July/Aug 2012 Issue
- Hall Table with Flair by Jennifer Anderson #236–Nov/Dec 2013 Issue
- Display Cabinet, the Krenov Way by Jim Budlong #208–Nov/Dec 2009 Issue
- Mid-Century Credenza by Libby Schrum #261–May/June 2017 Issue
- Get perfect reveals with a Domino by Anissa Kapsales #261–May/June 2017 Issue
Question 2:
How do you ensure a square glue-up with a leg that tapers just below the apron? Are you relying completely on the shoulder of the tenon being square? -Aaron
Segment: All Time Favorite Technique of All Time… for this week
John – A simple wooden mallet
Mike – A sharp tool
Ben – New hand tool rack with magnets inlayed to hold tools
Question 3:
My question is about dust collection. Before getting into this, I had no idea people put so much effort into dust collection. I started woodworking with my Dad years ago, and we just rolled the table saw out into the driveway. These days, I have a shop vac hooked up to a cyclone that I use for whatever I can, but my dust collection isn’t great. I end up wearing a respirator most of the time, except when i’m doing something that doesn’t produce dust, like hand planing.
How much importance do you place on having good dust collection, and is there ever a point at which your dust collection is so good that you don’t feel the need to wear a respirator? If not, what activities do you put a respirator on for? -Andy
Recommendations:
John – Don’t freak out when you make a mistake, just Tetreault it!
![]() |
![]() |
Every two weeks, a team of Fine Woodworking staffers answers questions from readers on Shop Talk Live, Fine Woodworking‘s biweekly podcast. Send your woodworking questions to shoptalk@taunton.com for consideration in the regular broadcast! Our continued existence relies upon listener support. So if you enjoy the show, be sure to leave us a five-star rating and maybe even a nice comment on our iTunes page.
Comments
Thank you for giving Matt Kenney the shout out at the beginning. I loved his work on the magazine and the podcast and he was one of the people that made Fine Woodworking Live so much damn fun these past two years. I have a pretty large circle of friends and acquaintances in the woodworking world and we were all pretty saddened to hear of his departure. I know it's tough times to be in the publishing business but I'm not sure why Taunton would dismiss such a vibrant and dedicated personality from its ranks. I still love Fine Woodworking but it was very disappointing to hear. I hope both Matt and FWW thrive in the future.
What a cryin' shame! I second kevin0611's comments. I will miss your presence on Shop Talk Live and I'm glad I've got your book to enjoy, Matt. Best wishes to you!
Going to miss Captain Snark.
Adios Matt, I'll miss your contributions to the podcast and the magazine. Love your book.
The picture of Ben's shop/tool holder and window were nicely done and made me wish I had a window like that in my own shop. Fortunately you provided the picture image inserted into the video so that we didn't have to look at it on the the screen on the wall where the picture was marred by the presence of those unconscionably large microphone stands . . .
Welcome John! So long Matt!
Regarding dowel jig vs biscuit joiner, the uses discussed don't capture the biggest difference between the two: a dowel jig can join just about anything that a domino can join, and do it incredibly strongly for a fraction of the price. A biscuit joiner sucks at joining things that require strength. In fact, it's not recommended, and this was like comparing super glue to hot glue.
Take a look at the JessEm doweling jig, which has you index placement of the dowels to various lengths off a reference edge (allowing for uneven thicknesses of panels if necessary--and as is common in hand tool work--, and placing aprons etc a set distance from the edge of a leg). There's also a stupid-simple alignment function to match the exact placement across panels. If you don't know precisely what I mean, look it up because I don't think people really appreciate how game-changing these two attributes are for a doweling jig. For example, when I use it for panel glue ups, the centering slot makes for dead simple, exactly placement of dowels on joining boards.
This jig is one of the best purchases I've made-- a saver of time, headache, and lots of money. When I'm too lazy to do mortise and tenon, I do dowels for a fraction of the price and functionally the same strength as a domino. The JessEm marketing material (or DowelMax?) has some published strength tests, but what does marketing material mean anyway? If you do the surface area glue math, you'll find that yes, they are roughly equivalent if you have machine-like dowel holes (which they are, every time).
Anyways, I'm saddened to hear that Matt K has been let go. He will be very missed. With all the changes in the last year, I'll have re-evaluate whether my subscription is worth it. We'll see how the next couple of issues go...
I'd like to tell you I enjoyed the episode. Truth be told, I was in shock throughout the episode with Matt getting laid off. I am sure he will be fine but still.
By the way, I still get annoyed that the 49ers traded Joe Montana. Even if Steve Young was the benchwarmer.
Woodworking was a refuge, a quiet place to go after a stressful work day. For 40 years at my day job I lived with value analysis, streamlining, downsizing, re-engineering, right sizing and then outsourcing.
Now all that rubbish has begun to mess with the peace and tranquility of my hobby.
But just as there was no silver bullet for my employer, in this age of social media there isn't one for Taunton either. Old fashioned print media are produced anonymously, podcasts and social media are not. At least one FWW staffer has more Instagram followers than the actual magazine ( and more followers than the magazine has paid subscribers ) Inspired woodworkers like Matt are real sources of value to FWW, even though FWW may not understand.
My interpretation was that Matt was one of FWW's most valuable assets. Meticulous woodworker, very competent in video presentations and great on the podcast. Im shocked to hear he was let go.
To user-7069574, you will notice the Ben mentions that he edited the question. I'm the one who wrote in with it. As a matter of fact, I asked about the JessEm specifically in the question because I didn't think there was much difference between a properly done dowel & a floating tenon. Your thought process paralleled mine. I understand they had to edit the question for space. You have given me good feedback and room for thought.
I think the hosts gave me food for thought in a different direction too. I have a lot to consider as to what direction I take. It's interesting how they all end up making their own jigs.
BTW, the project that most inspired the question was the Kevin Rodell's Limbert inpsired coffee table which uses biscuits liberally. Clearly in that design they are used more for registration and alignment than for outright strength. But I was hoping more for both alignment and strength. There are more variables at play than I realized at first. Much to learn.
I too will miss Matt Kenney's snark!
Dammit. Just Dammit.
Please keep us informed re: Matt.
Issue No. 269 will be a keeper, especially if it turns out to be the last issue that Matt Kenny is highlighted in as a staff member. Matt has been a wonderful source for insight and his petulant opinions have added much needed levity to the normal nerd-laden woodworking jibber jab.
When I discovered the Shop Talk Live series, I quickly dove into the podcast archives. What I discovered was a light-hearted forum for sharing, professional instruction from the folks who decided to make woodworking their life’s path. Dogma meets dharma!
The Ed, Asa and Matt podcasts are priceless, there is a levity in them that is real and inviting. As a new subscriber to both FW print and web, my hope is that Matt continues to contribute to Taunton’s publication offerings, as a guest editor and/or writer-at-large.
With change comes opportunity!
Log in or create an account to post a comment.
Sign up Log in