Ebonizing Wood with Steel Wool and Vinegar
This steel wool and vinegar method for ebonizing wood is appropriate whether you want a dark, graphic look or tones of gray, blue, and purple
Ebonizing wood is a wonderful way to create a dark, graphic look that emphasizes the form of a piece. The steel wool and vinegar recipe I use gives depth and darkness to heavy-tannin woods like walnut and oak, while still allowing for aspects of the grain to shine through. Since this is a reactive finish, it penetrates deeper into the wood than a stain or dye that sits on top, creating a natural, durable black tone. On low-tannin woods, it produces lovely grays, blues, and purples. The ingredients cost very little and can be bought at any hardware and grocery store. You can easily experiment and develop a recipe that’s right for you.
Make the solution: Cleaning the steel wool
The recipe calls for a 12-pad package of No. 1 steel wool, a gallon of white vinegar, lacquer thinner, and a few clean containers. The goal is to make the purest solution possible, so I remove the excess oil that’s present in the steel wool by rinsing it in lacquer thinner. I use a three-container method, rinsing the steel wool in consecutive containers, each with a few ounces of lacquer thinner in it. The first container is the dirtiest, and by the time it reaches the third, the steel wool should be relatively clean. Once I’ve cleaned a full bag of steel wool, I store the used lacquer thinner from the two cleaner containers for future use. I discard the dirtiest batch of thinner.
Making the solution: Add the vinegar
Set aside the pads on a clean surface for about 20 minutes to allow the thinner to evaporate. Clean a bucket (the cleaner the better) to make the solution in. I have a specific bucket that I use only for this process. Place the clean steel wool pads in the bottom and carefully pour the gallon of white vinegar over them, making sure the pads are completely submerged. The solution should begin to bubble, a sign the vinegar is reacting with the steel wool and beginning to break it down. I stir the solution every couple of hours, making sure that the steel wool is still submerged in the vinegar. I allow the solution to brew for 24 to 36 hours, stirring occasionally when possible.
Once the time is up, I strain the vinegar solution into a clean container through a few layers of fresh white rags. If my cleaning process was thorough, the strained solution should be perfectly clear or close to it. The leftover steel wool can be discarded at this point. The solution is ready for use immediately after straining.
Brush on the solution
Once the piece has been sanded up through the grits to 220, I raise the grain with water, wetting the wood’s surface evenly. To keep the ebonizing solution as pure as possible, I pour what I need into a smaller container before applying it. To help the solution penetrate deeper into the wood cells, I add one or two drops of dish soap to 8 oz. of solution. This helps break the surface tension of the liquid and produces a blacker, more consistent result, especially in open-grain woods like oak.
While the wood is still wet from the water, apply the ebonizing solution liberally and work it into the pores with a stiff brush, brushing in the direction of the grain. Work in sections using overlapping brush strokes. The wood should begin turning dark almost immediately. One coat should do the job. After the first coat has dried, you may find a second coat necessary to even out missed spots, but it won’t darken the color much.
After I’m satisfied with the evenness and depth of color, I allow the wood to dry before sanding back any raised grain with 400-grit paper. On unfinished wood, this process will produce a deep navy blue color. Depending on what is desired, almost any type of finish can be applied now. I generally use a penetrating oil finish. It turns the wood from navy blue to rich black, for a classic ebonized finish.
Options for a blacker black
Brush on the solution Once the piece has been sanded up through the grits to 220, I raise the grain with water, wetting the wood’s surface evenly. To keep the ebonizing solution as pure as possible, I pour what I need into a smaller container before applying it. To help the solution penetrate deeper into the wood cells, I add one or two drops of dish soap to 8 oz. of solution. This helps break the surface tension of the liquid and produces a blacker, more consistent result, especially in open-grain woods like oak.
While the wood is still wet from the water, apply the ebonizing solution liberally and work it into the pores with a stiff brush, brushing in the direction of the grain. Work in sections using overlapping brush strokes. The wood should begin turning dark almost immediately. One coat should do the job. After the first coat has dried, you may find a second coat necessary to even out missed spots, but it won’t darken the color much.
After I’m satisfied with the evenness and depth of color, I allow the wood to dry before sanding back any raised grain with 400-grit paper. On unfinished wood, this process will produce a deep navy blue color. Depending on what is desired, almost any type of finish can be applied now. I generally use a penetrating oil finish. It turns the wood from navy blue to rich black, for a classic ebonized finish.
Options for a blacker black
One option for producing an even darker result is pre-treating the wood with strong black tea, which is rich in tannins. This can be brewed and applied to the raw workpiece before the ebonizing solution. The heavy concentration of tannins, combined with the wood’s natural tannins, produces a blacker black. Another approach I use is to apply an ebony tung oil after the ebonizing solution but before the final topcoat. This product, made by Sutherland and Welles, has an aniline dye base mixed with tung oil and helps to even out any unwanted light areas or high contrast. While it does make the wood slightly warmer in tone, it produces a beautiful finish and is a great option.
Works on tannin-light woods, too
I often use a steel wool and vinegar process on maple and other tannin-light woods, but I call it oxidizing instead of ebonizing. Oxidizing uses a lighter solution, which you can get by diluting the ebonizing solution with water or vinegar, or making a different solution with about half the amount of steel wool as the original. All you want is a slight reaction.
The most difficult part of oxidizing is choosing the finish that will go on top of it. Anything oil-based will amber the wood, turning the beautiful cool colors muddy and green. You want a finish that doesn’t change the color of the wood, so you can keep those blues and grays. I’d suggest a water-based spray finish for this.
From Fine Woodworking #275
To view the entire article, please click the View PDF button below.
More on FineWoodworking.com:
- An Exploration in Finishing – A modern take on jin-di-sugi and ebonizing by Kevin Rodel, Anissa Kapsales #196–Jan/Feb 2008 Issue
- All About Dyes and Stains by William Duckworth
- Should Woodworkers Say Goodbye to Ebony?
Fine Woodworking Recommended Products
Bumblechutes Bee’Nooba Wax
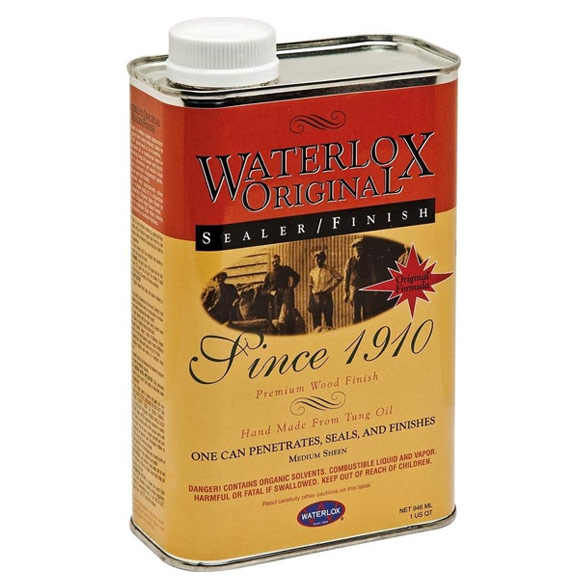
Waterlox Original
Foam Brushes
Comments
I'm curious if anyone knows what gas is being emitted when the mixture begins to bubble. Acetic acid and steel? CO2 is my first thought, but I don't really know
NRH39 is correct. The answer is hydrogen.
I would have thought it wolud be hydrogen - but high school chemistry was decades ago ;o)
Maybe it’s just air trapped in the wool?
Log in or create an account to post a comment.
Sign up Log in