Light, Sturdy Dovetailed Tote
Inspired by a traditional tool tote, dovetails and tenons combine for sturdy, lightweight storage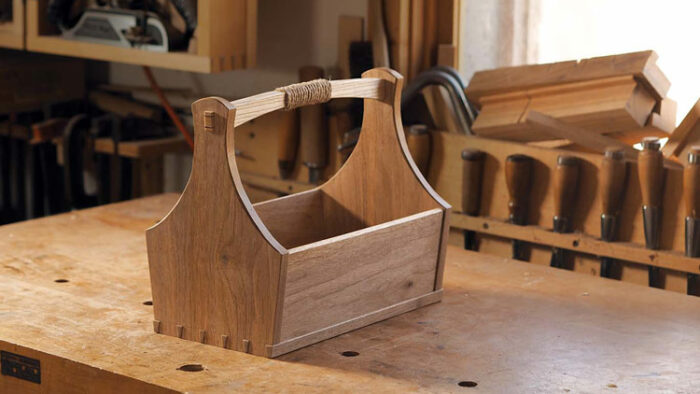
When my wife, Rachel, said she needed a small basket to hold mending supplies, I decided that the traditional tool tote was the perfect inspiration for the project. The form has been around for hundreds of years and comes in many sizes and variations. It’s a versatile design that can be expanded to fit any need and use you may have.
For this tote, I decided on dovetails to join the ends to the bottom, and through-tenons to secure the handle. The stub tenons on the angled sides fit into grooves in the ends. The result is a sturdy tote that offers some fun building challenges but won’t tie up your shop for too long.
Design is an important part of the building process even on simple projects. While I had an idea of how I wanted the tote to look, getting the overall size right was critical to its functionality in the future. Something too big and clunky, or too small to be useful, would find itself tucked away in a corner somewhere. So Rachel and I took a minute to walk through the house and look at boxes and bins to help determine a good size. I find an activity like this to be far more effective than asking for dimensions from a client. I then made a quick mock-up out of MDF and brought it into the house for a test drive. Once we had determined the final size, I was ready to mill up some lumber.
Dovetails and through-mortises before shaping
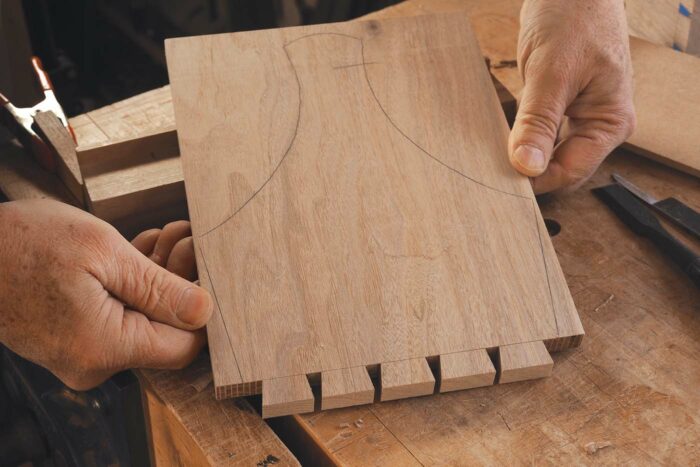
![]() |
![]() |
The ends are joined to the bottom with simple through-dovetails. To make the process easier, cut and fit the dovetails before the ends are sawn to shape. But consider the final shape of the ends when laying out the tails. A good way to do this is to draw the shape on one of the ends and then lay out the tails so that they are centered on the profile. It will look a bit strange until you cut the final shape. The dovetail pins and tails are proud of the surface. To accomplish this, set a marking gauge to roughly 1/16 in. over the thickness of the stock when scribing the base lines.
![]() |
![]() |
![]() |
After cutting the tails, transfer the tail locations to the pin board. Accurate layout is critical here. Applying tape to the end grain gets you off to a good start. By scribing through the tape and peeling it away from the waste areas, you are left with a clear roadmap for cutting. In addition, if you stray from your lines with the saw, the tape will serve as a guide for paring. The next challenge is to position the tail board accurately when scribing. A piece of 1/4-in. MDF clamped along the baseline of the tail board acts as an effective guide when positioning it on the end of the pin board.
Finally, strike a pencil line down the face of the pin board at each pin location. This provides a visual guide when sawing and will offer clues when paring the walls vertically during fitting. If it’s been a while since you picked up your dovetail saw, clamp an offcut into your vise, scribe some vertical lines down the face, and take some warm-up cuts; once you find yourself hitting your line more often than not, you’re ready to cut some dovetails. After sawing the pins, remove most of the waste between them with a coping saw or fretsaw. Then chisel or rout to the baseline, and pare the pin walls.
![]() |
![]() |
![]() |
![]() |
The first task when fitting the joint is to make sure that the walls of the pins are vertical. Out-of-square walls can cause the boards to split when you’re driving the joint home. If you know that the walls are vertical, you can be a bit more forceful when seating a joint.
With the dovetails complete, cut the mortises for the handle. To lay them out, first apply tape to both faces of each end. Then use a marking gauge registering off the sides of the board to scribe the mortise walls. You’ll use a 3/8-in. bit to drill out the waste before chopping, so lay out the mortises slightly wider than the bit to make it easier to avoid drilling outside the scribe lines. Once the waste has been drilled out, chopping goes quickly. Work halfway in from each face to ensure clean surfaces.
Once the ends are mortised for the handle, it’s time to saw them to shape. The tote sides will be tenoned into grooves that run parallel to the end boards’ angled edges. To simplify grooving, it’s easiest to cut the angles first and then use them as a guide when routing. The exact angle isn’t important; however, it is critical that the angles on both ends match each other. A simple approach is to tape both ends together when cutting them out. After bandsawing to the layout lines, use a hand plane to true the angled sides. Smoothing the curves can be tackled with a file, a spokeshave, sandpaper, or a combination of all of the above.
I don’t have a fence for my small plunge router, so I attached a guide block to the base. Make a full-depth plunge at each end of the groove, and then rout the groove with multiple shallow passes.
To trim the bottom to final width, dry-fit one end to the bottom. Place a 1/16-in. shim against the edge of the end and pencil the final profile on the bottom. Tilt the table saw’s blade to the same angle as the sides to rip the bottom to final width.
Cut the stub tenons on the ends of the sides at the table saw. Dry-fit the tote bottom and ends to measure the shoulder-to-shoulder length of the sides. Use a dado blade set wider than the desired tenon, and overlap a portion of it with an L-fence clamped to your rip fence. Using the miter gauge, start a bit too long, and sneak up on the final length by adjusting the rip fence. To cut the angled edge along the bottom of the sides, tilt the blade to match the angle of the ends. The top edge is left square and rounded with a block plane.
The handle completes the tote
While the other parts of the tote are made from butternut, I used ash for the handle. The color contrast is nice, and ash is a tougher wood, allowing me to give it a thinner profile while maintaining strength.
![]() |
![]() |
Cut the tenons and the recess for the cord wrap before cutting the curves. Once again, you’ll need to sneak up on a final length. I like to end up with a tenon that extends farther from the face than the dovetails do, approximately 1/8 in. This allows me to angle the end to match the radius of the handle’s curve. It’s a small detail, but a nice one. Once the tenons are complete, use a dovetail saw to kerf them for wedges.
The top and bottom curves of the handle have different radii. Using a curve with a smaller radius for the bottom edge results in a handle that is narrower at the center than the ends, giving it a lighter, less clunky look. It’s a technique that I use often in my work. After bandsawing, clean up the curves with a block plane, leaving heavier facets that will add a tactile quality when someone lifts the tote.
![]() |
![]() |
![]() |
![]() |
Once the curves are complete, cut shallow cord recesses along the top and bottom edges to match those on the faces. The 1/16-in. recess provides a nice seat for the cord, which I add after applying a coat of shellac to the handle. Using 4mm hemp cord, begin the wrap by trapping the end under the first five or six wraps along the bottom of the handle, and then trim it with a knife. Continue wrapping the handle, stopping four or five wraps short of the far end. Bend a short length of baling wire into a U. Hold it in place along the bottom of the handle and continue wrapping over it. Once you reach the end of the recess, thread the end of the cord through the U in the wire and use a pair of pliers to pull the wire under the wrap, pulling the cord end with it. Slip a knife between the wraps where the cord end exits to trim the end of the cord. Be careful not to nick the wraps.
Finish first, then glue
On a small project like this, you can usually get by with applying two coats of thinned blond shellac. If you’re working from a can, thin the shellac 1:1 with denatured alcohol. Plane or sand the parts to at least 400 grit, and wipe on a coat of shellac, steering clear of glue surfaces. Once the shellac is dry, which won’t take long, give the parts a quick sanding with fine sandpaper to knock down any raised grain. Then apply a second coat of shellac. I usually stop here on a project like this. Feel free to add another coat, but be careful to avoid building a surface that is too glossy. To my eye, it doesn’t fit the look of a utilitarian piece like this. If the surface does get a little shiny, wait until the tote is assembled and then add a coat of paste wax using 0000 steel wool to tone down the gloss and create a satin sheen.
Glue-up is a little tricky because everything must come together at once. I don’t flush the joinery after gluing, so I try to minimize squeeze-out. On the dovetails, apply glue only to the side walls of the pins. Add a dab of glue to the grooves in the ends, but not the side tenons themselves. The tenon on the handle is a through-tenon, so apply glue only to the tenon and not the mortise. When you’re applying glue to the tenon cheeks, try to work a little into the wedge kerf while you’re at it.
![]() |
![]() |
For glue-up, lay one end flat on the bench and insert the bottom, handle, and both sides. Then add the second end. Make sure the side tenons are aligned with the grooves before trying to seat the ends fully. When clamping, make sure the sides sit flush to the bottom. Wedging the handle won’t pull the joint tighter, so make sure the sides are clamped flush to the handle’s tenon shoulders before driving in the wedges. After the glue dries, trim the wedges and sand them flush. Any areas of squeeze-out should pop off easily from the finished surfaces with a chisel. Add a light spot coat of shellac where needed.
Michael Pekovich, Fine Woodworking’s editor and creative director, teaches woodworking around the country.
Fine Woodworking Recommended Products
Suizan Japanese Pull Saw
Comments
Where is the PDF button to select to print the article?
Ditto. Good luck.
Hi. I've attached the PDF so you should be able to download it now.
I've made the PDF downloadabel now, at the bottom of this page. Thanks for letting me know.
It comes up as PNF. Page not found. Merry Christmas everyone or whatever you celebrate.
PDF not working.
Will we ever see a video series of this? Love seeing and hearing Mike in action!
I just enrolled in Fine Woodworking thinking I could download plans such as these. I really like paper copies of the project rather than viewing a webpage while in my shop! Please let me know if I'm doing something wrong when trying to download the pdf of this project.
Thank, Dave
I'm also looking for the PDF option.
This will be a great exercise for a woodworker looking to move up a notch.
I will enjoy making this tote, and I have some butternut from VT already!
Kiwi Pierre
Hi there!
PDF is updated and should be working fine.
I second a video series.
PDF works, thanks.
Simply elegant!
Log in or create an account to post a comment.
Sign up Log in