Glazes and Toners Add Color and Depth
Layered finishes allow correction, enhancementSynopsis: By adding colored finish layers at the right time, you can alter or compensate for an existing color as you go, getting exactly the right result. Two finishing products, glazes and toners, let you do this. David E. Colglazier explains their differences and how to layer them. He uses them for restoration jobs and color matching, mostly, and he explains how to lock in a layer with a barrier, such as nitrocellulose lacquer or shellac. He talks about applying and manipulating glazes, and how toners are sprayed on and left to dry. Side information offers a glossary of common colorants and on color matching.
Many woodworkers assume they’re committed to storebought stain colors. For some finishing jobs, though, a one-time application of stain just won’t do. But by adding colored finish layers at the right time, you can alter or compensate for an existing color as you go, getting exactly the right result. Two finishing products, glazes and toners, will let you do this.
Glazing and toning can add depth and color to a finish or adjust the hue to get the look you’re after. I rely on both methods in my antique-restoration work because there’s no other finishing process I’m aware of that can bring such subtle refinement or dimension to a finish. Despite their similarities, glazes and toners are used differently.
Glazes rely on an applicator to add texture or simulate grain detail. It helps to think of glazing as painting (see the photo below) because you’re covering, or at least partially obscuring, a base color of some kind. Glazes usually go on just before the topcoats so that you won’t disturb or cover up the brushstrokes.
Toners are generally not manipulated with a brush or rag after they are applied. Think of toning as applying thin layers to alter the overall color of a piece. Spraying is best.
Glazes and toners are great for refinishing, restoration and color matching, but they aren’t for every job. They require more artistic skill than other finishing methods. With glazing and toning, you need to know how to spray a finish. You often have to lock in a layer of glaze or toner by spraying a coat of nitrocellulose lacquer or shellac. If your shop isn’t equipped to do this, you can use aerosol cans of lacquer (made by Deft) and shellac (Wm. Zinsser & Co.), which are readily available.
Layering is the key
The human eye is a very perceptive tool. With training, it can observe at least five variables of a finish: surface defects, wood-pore and flat-grain color, finish depth, topcoat sheen and texture. Glazes and toners rely on the eye’s ability to perceive depth. By visualizing what the final result will look like two or three steps ahead, I can plan glaze and toner layers that will compensate for or correct a hue that isn’t quite right. (The story on p. 79 gives a brief explanation of color matching.) Each layer, whether opaque, transparent or somewhere in between, affects the final color, texture and readability of the underlying wood.
From Fine Woodworking #116
For the full article, download the PDF below:
Fine Woodworking Recommended Products
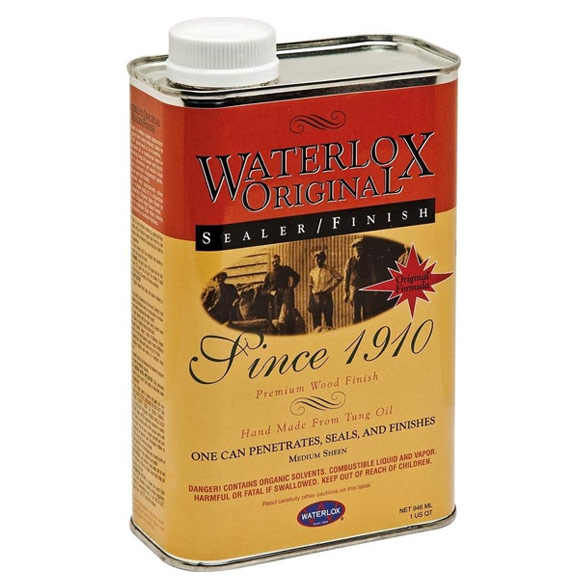
Waterlox Original
Odie's Oil
Osmo Polyx-Oil
Log in or create an account to post a comment.
Sign up Log in