Dust-Proof Any Table Saw
Enclose the saw, direct the dust, and you'll clear the airSynopsis: Retired pilot Richard Babbitt has figured out how to harness the power of airflow to keep his workshop free from dust–specifically, to ensure that the dust from his contractor’s saw goes into the collector and not his lungs. By closing off most of the saw with wood panels and allowing air to flow rapidly through a few areas, he has managed to capture most of the dust from his tablesaw and keep the motor cool in the process. Intrigued with his ideas, two Fine Woodworking editors applied his principles to a hybrid saw and an old cabinet saw with equally impressive results.
From Fine Woodworking #205
As a retired pilot living in Washington State’s San Juan Islands, I often fly cancer patients to the mainland for treatment. Having witnessed the plight of these patients, I became earnestly motivated to minimize dust in my shop after the government categorized wood dust as a carcinogen.
The major dust maker was my contractor’s saw, one of an estimated million such saws in this country. Manufacturers seem to have given little or no thought to dust collection beyond sticking a dust port below the blade. The inefficiency of this system is obvious every time a piece of wood is cut and the operator becomes surrounded by a cloud of dust. To come up with a better solution, I put on my pilot’s cap and began to think about airflow. By applying aerodynamics to my tablesaw, I was able to vastly improve its dust collection, and keep the motor cooler in the process.
While I’ll focus on the contractor’s saw, the principles and techniques work on any saw. Two of Fine Woodworking’s editors will describe how they dust-proofed a hybrid saw and a cabinet saw.
Dust goes with the flow—if you direct it: The average contractor’s saw, with its open design, is equivalent to sticking the dust hose in the middle of the room. Some dust-laden air will be drawn in, but the majority will be too far from the hose and will float off into the shop. You need to increase the velocity by restricting and directing the amount of air entering the base of the saw. My plan uses three pieces of plywood to enclose the lower part of the saw, and five more to build a small box around the rear-hanging motor. This enables me to direct the airflow to the dust port.
This system requires a dust collector rated at a minimum of 1,100 cubic feet per minute (cfm). Most 1 1⁄2-hp mobile dust collectors fit the bill, but if yours doesn’t have a 1- or 2-micron filter, you should invest in one. The smallest particles are the most dangerous.
Begin by enclosing the motor—The motor enclosure is suspended from an outfeed table. The bracing under my Rockler table is placed almost perfectly for this installation, but if you have another outfeed table, you can either adapt the bracing or attach a shopmade frame to the underside of the table.
The first step is to calculate the size of the box required to enclose the motor at both the 0º and 45º blade settings. On most contractor’s saws, the motor is mounted on a hinged plate and hangs down behind the saw, supported by the drive belt.
For the full article, download the PDF below:
Fine Woodworking Recommended Products
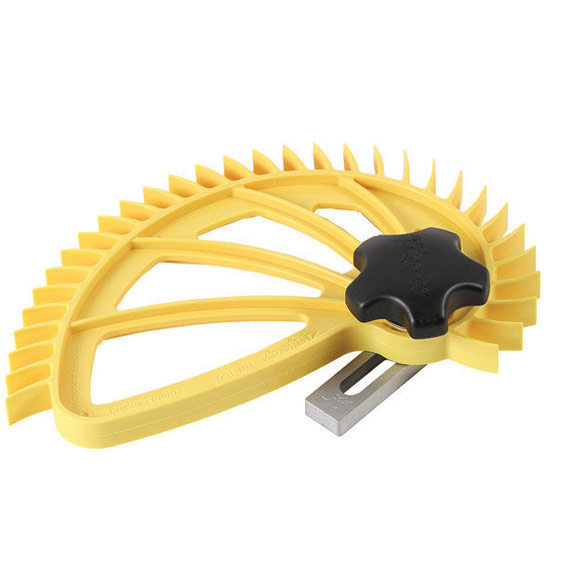
Hedgehog featherboards
Milescraft 4007 6in Bench Clamp
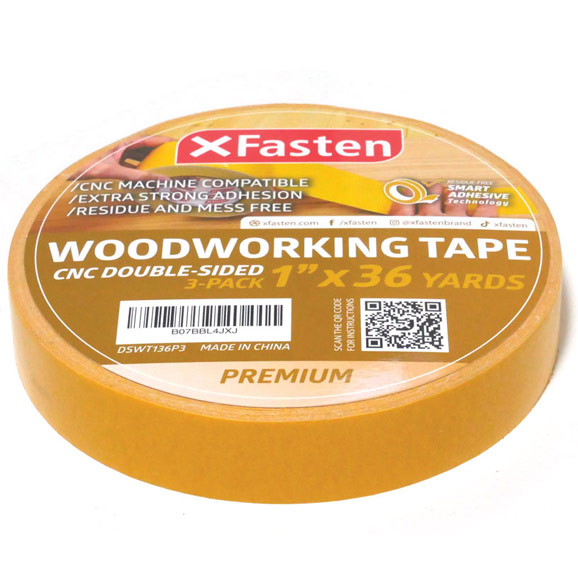
Double Sided Tape
Log in or create an account to post a comment.
Sign up Log in