Can you advise on building a single screw veneer press?
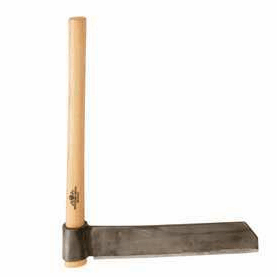
Little boxes have become a regular feature in the shed. I’m at the stage where I’d like to progress them beyond the basics to include some of the more fancy effects, particularly the use of nice veneers.
Various veneer-related tools have been accumulated but I lack a veneer press. I’d like to try all the various methods of sticking veneer to a substrate – hammer, vacuum bag and press. There’s a veneer hammer in the shed and the small plastic bag of the kind that can be used to make a vacuum press – but no press. There is, though, a humongous York single screw coming in the post, with a beefy acme thread meant for use in a press.
At present I’m looking at book binder press designs, as there seems to be a lack of single screw designs for veneer presses on the interweb. I’m assuming such a design would need to be beefed up compared to a true book binder press, though …… ?
At the moment I’m thinking four 50mm diameter beech corner columns with 10mm threaded rod through them to connect a 50mm thick top to a 50mm thick bottom, both of birch ply, faced with 5mm thick mild steel sheets. The top (movable) pressing part would be similar but have some sort of surface to press on the veneered part. The area will be 12″ X 12″ or thereabouts, as this will cover all the sizes of parts I want to veneer for little boxes.
Anyone have any experience and/or advice on the details of such a design?
For example, do the surfaces that press on the veneer and underside of the substrate need to be not just glue-proof but dead flat? Or is it better to use something like a hard rubber surface that can deform slightly to press into any slight dips or hollows on the workpiece, as well as on the peaks, even if these bumps & dips are just a fraction a millimetre?
Lataxe
Replies
I've never done this, but reading your question reminded me of this video:
https://www.finewoodworking.com/2008/11/06/shop-made-veneer-press
I mainly use a vacuum press for veneer panels (I mainly do marquetry).
So I look forward to the results of your exploration with pressing.
You raise an important point in the last paragraph of your post, regardless of how the pressing is accomplished. The commercial veneers I use are 0.55mm, plus/minus .05 to .10mm. Incorporating a number of different veneers into your panel (as is certainly the case for marquetry) can result in the thicker pieces pressed firmly onto the substate while the thinner pieces may not be.
So when doing marquetry pressings or combining a number of different veneers in a pattern onto a panel, I do what Paul Schurch does, which is to use a top and bottom platen and make a sandwich before pressing.
The sandwich recipe is as follows from bottom to top: bottom platen, a layer of canvas, a layer of polyethylene plastic, the veneer panel, a second layer of plastic, another layer of canvas and the top platen. After removing the sandwich from the press you will see and feel the resultant topography from the minor thickness variations of the veneers. This is confirmation that all pieces, regardless of thickness are evenly and firmly pressed onto the substrate.
Cheers
For numerous small jobs,chair backs,box tops,small inlay,I use a book press that is so heavy I can barely lift it.For curved parts such as chair backs ,I make male and female hard rubber lined cawls.
I have a book press found it in the trash ,works wonders for veneer and all sorts of glue ups
Thanks all for your replies.
It sounds like a design for a veneer press to handle small pieces like those in little boxes can successfully emulate that of a good book press, then, since two of you are actually using a book press for veneering. I'll find a beefy example and copy the design, I think.
I did consider buying a good book press but those good ones of beefy aspect cost a lot, even second hand. (And the second-handers also look like they need a substantial refurbishment). The less expensive newer ones look too flimsy for squishing veneer to substrate, though - thin aluminium panels and rather basic screw.
From what two of you say, it also seems that the flat part actually pressing on the veneer needs to have some ability to conform to the very small height differences likely to be present when veneered parts are pressed to even the flattest of substrates. But perhaps the canvas & polyethylene sandwich is better than a rubber sheet or similar as such a sandwich isn't a permanent part of the press itself, so can be readily renewed, varied or otherwise adapted to a particular workpiece.
Lataxe
Hello Lataxe,
If I had one of those book presses I would certainly give it a go. Seems critical that the platens are not only dead flat and stable but also perfectly parallel to one another for pressing veneer.
The great veneer master Silas Kopf used a variation on the book press. His press had multiple screws pressing down on cauls which in turn distribute pressure across a top platen.
I considered building a scaled down version with 4 screws and 2 cauls and then of course, I realized that I would get the exact same result on smaller panels by simply using regular woodworking clamps and cauls. For even smaller pieces I skip the cauls and use as many clamps as I can fit around the perimeter of the platens as long as I can get one on the centre. I use this method if I am too lazy to set up the vacuum press (which is most of the time) and I get very good results.
Cheers
Here's a picture of a small press I use. The area is about 14" x 32". For motive force, you are much better off with hydraulics rather than a mechanical screw. This is a 20 ton jack that will produce about 100psi over the 3 square foot press area. These are inexpensive. The main challenge is turning the concentrated force of the jack into an evenly distributed force. This press has plattens of 4" thick laminated strand lumber.
The even distribution of the pressure from the device applying it seems to be a fundamental aspect of a veneer press. As I understand it, the vector of the forces from a pressure applying "point" will radiate out through what it's pressing on at around 45 degrees from the vertical, in all directions - if the stuff being pressed is perfectly stiff.
As most stuffs are not perfectly stiff, the objective seems to be that the press design must make the "stuff" as stiff as is practicable. Some seem to use immensely thick platens of relatively stiff-stuff, such as 3 - 5 inches of glued up plywood or a dense and inherently stiff lump of hardwood. Others use the caul method to make the applied pressing force radiate out in a wider fashion.
Given that veneer can be applied successfully without much pressure at all, via use of the veneer hammer, I wonder how stiff and flat a veneer press platen must be to be effective? Some devices do seem like overkill ..... but it would be useful to know of the experiences of press users about any untoward effects from failing to get enough pressure and/or failing to have the platen sufficiently flat. What is "enough pressure" and how flat is "sufficiently flat"?
Not easy to answer, I know, since substrates, veneers and even glues vary, so perhaps the only sensible answer is "sufficient to stick the veneer on with no blebs, buboes or pustules. :-)
Lataxe, still collecting press parts (got the ginormous screw now).
Bad glue lines are the end of the world in a veneered piece.
You can get an ok glue line with plenty of glue and little pressure, relying on the tack of the glue.
The strongest glue lines use very little glue and high pressure. This gets progressively more challenging to do. People do choose to not get real wound up in this.
A common mechanism for distributing pressure is a sprung structure under the platen that applies force to the perimeter first and then to the center as it flexes. I use shims on the ends of the steel tube under the lower platten.
Lots of people get good results out of vacuum presses that work at about 15psi. In industry, pressures started at about 50 psi in glue rooms I worked with.
Hello John,
Various book binding presses seem to have an arrangement of one sort or another for better distributing the pressing force, as you describe. It makes sense to have a platen that works like a caul, to initially transfer "press" to the outside edges of the platen but gradually press also towards the centre as the pressing force is increased and any slight hollow of the platen is pressed to flat.
I have a Veritas router table that has a 1/4" steel sheet as the table, with a slight crown built in, so that when the weight of a router is hung off it the crown in pulled flat. It's a very small crown but even after 20 years, the table is still dead flat with the router in.
But how does one find such a crowned (or hollowed, viewed from the other side) steel sheet to use in a veneer press I wonder? Something that will transfer initial "press" to the periphery but go flat as the force increases.
I suppose it may be possible to make a wooden version of such a platen, by planing out a slight hollow on the down side / pressing side. The amount to hollow would be a guess, though.
There are designs of book press using arched arms that connect to the pressing platen at the four corners, so that the outside edges of the platen get pressed first then (presumably) transfer some of the force to the centre of the platen. That too looks like a guessed-at force-transfer design, though.
****
All these points are helpful in thinking about my eventual veneer press design, though.
Lataxe
This forum post is now archived. Commenting has been disabled