Compound miter settings for Bow Arm Morris chair
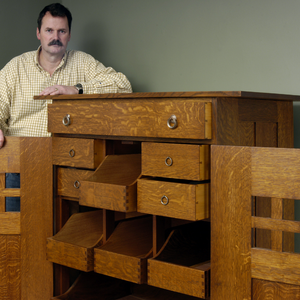
I am almost finished building the bow arm Morris chair from the American Furniture Design plans and Gregory Paolini’s tutorial. All is going according to plan but I am now stuck on one problem: what are the miter and compound miter settings for cutting the pyramid top on the back leg through tenon.
Gregory explains well how to cut the front tenon but then does not provide enough explanation of how to cut the rear. It must take specific settings for the miter gauge and table saw blade angle in order to get a perfect pyramid shape cut that lines up with the curve of the arm at the back.
I would love it if anyone can help me with this. Many thanks in advance.
( by the way I did search through the Forum for answers to this question but there are so many posts about this chair and I wasn’t successful in finding an answer. My apologies if this is a repeat.)
Rich
Replies
Hi Rich, It's time to take a plunge. What you are faced with is handwork. Make up a section of matching tenon and practice a few times before tackling the actual chair leg. I'd go with chisels, but this whole thing could be done with sandpaper glued to a stick.
Set yourself up with a peg stop or something to give solid contact underneath and practice marking, cutting, and shaping the pyramid. Mark the front face on material below the surface inside the joint. You'll need 3 lines on the through tenon... the baseline scribed from the arm, an elevation for the the thickness to match the front legs, and a peak line where you'll cut off the top when you start.
Pencil marks across the corners and across the centers will help you gauge elevation as you begin to remove material. Re-mark if you need to as the lines get shaved away. All material removal will be from the perimeter towards the peak to avoid blowout on the edges.
If you get a perfect practice piece and botch the chair leg you can always cut it off and glue in the cap, hiding the fix until you just HAVE to tell someone.
Good luck!
Thanks MJ!
That's a very good plan and quite doable. However, my obsessive brain wants to solve the table saw method that Gregory Paolini refers to in his video:(https://www.finewoodworking.com/project-guides/chairs-benches-and-stools/9-prep-for-assembly ).
There seems to be a sequence of cuts that can produce an accurate result-- it's just that I haven't figured them out. The faux tenon option is always there too, but I succeeded in getting a near perfect M&T on all four joints (and that wasn't easy) so I'd rather be able to tell everyone that! :)
Anyway if I can't figure this out I will follow your good advice!
Thanks again.
McLaughlin uses a block plane in much the same way mj explains above. I agree that hand tools show the craftsmanship in the piece.
I watched the video,... he did not "show the work" as a long ago math teacher would have said. In truth I don't think he could afford to because every set of bow arms will be different off of the form. No doubt many test cuts and cusses went into that few seconds of video.
Starting with his 15 degrees callout for the front leg you could do drawings and work it out I suppose. Mill a few test pcs and go for it.
Thanks for all the feedback folks!
So as it turns out I've given up on the table saw route! (Even though my stubborn brain still wants to solve the problem)
But in the end, a sharp block plane gets the job done quite easily and quickly. And I can boast that I did it by hand now!
Here's a pic of a quick and dirty effort on a test piece.
Thanks for weighing in.
Rich
So here is the final result.
I actually went with legitimate through tenons in the arms front and back. And I cut the back ones by hand. Thanks for weighing in everyone!