Need help need to build wood curved mantle for my fireplace.
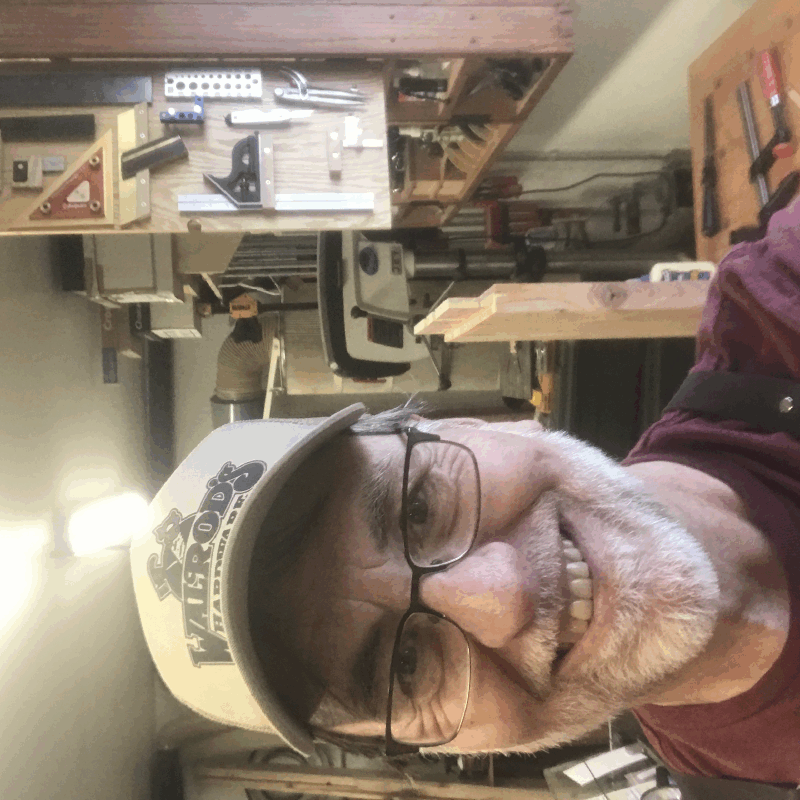
My Wife wants a wood mantle added on the curved brick mantle on our existing fireplace. She wants tradition looking mantle crown moulding front that angles down from shelf. The shelf is 84 inches from corner to corner. Center of mantle is 8 1/2” from the front of the brickyard to the back of the shelf. The ends are about 5 1/2”from the back of the shelf.
Any suggestion where to start on building this mantle is going to be really appreciated.
It is going to be built with red oak wood and moldings..I don’t think moulding will bend that much. Any ideas or suggestions would be greatly appreciated. I attached picture of fireplace.
Help.
Thank you, Jim
Replies
I would start by scribing a template of 1/4 or 3/8 mdf to the find the arc that will fit the brick face at the back of the shelf. From there there are a couple days you can determine the front face arch or radius. Building the shelf once you know the arc/radius should be straight forward. The shelf template can also serve to give you the arc/radius of the crown molding. As to the curved crown molding there are a number of ways to fabricate it but none of them are easy and depending on the size require either a molding machine like a Williams and Hussy or a shaper with custom knives Either of which if you don't already own aren't inexpensive. You can purchase a crown molding resaw it into thin strips then laminate it back together using a curved bending jig but that has a whole other series of problems Or that same molding could be stream bent using a similar bending jig. Both of these methods are labor and materials intense. Not knowing your shops capability or your experience level it's hard to say which of these ways to recommend
Thank you. I don’t have a shaper only a router table. Resaw I could do. Steam I could try. I have enough clamps. Do you think 8 inch red oak crown mounding would steam bend ok?
OK. What I didn't mention in my first response was you will need to make a design sketch of the piece. Other than that your just doing a lot of hand waving. Trying to communicate your design desire is very difficult as evidenced by the other responses So back up and make a sketch. Often the sketch will point out how the piece has to be built. Lots of folks want to know how to build first but mill shops pros will take the opposite approach and want a concept or design sketch first. After you have the sketch you can proceed to the next step.
Back to the curved crown molding. You probably should contract the crown molding to a mill-work shop. It only makes sense if you don't have the equipment. Before I retired I worked for a custom millwork and cabinet shop in San Francisco. We were small enough to handle one of a kind small orders like this. We would often take a project that consisted of fabricate only and leave the install part to the contractor or in this case you. Much of the work involved reproducing Victorian period molding, vertical and horizontal. So these kind of jobs came along all the time. Without a shapper or molder, milling the final profile is impracticable. It can be done by hand but that is probably the most skill intensive method.
Fortunately, you can build the shelf with simple power tools ie; jig saw, skill saw, and router or if you have them, a band saw, table saw and chop saw. So leaving the crown molding aside I will assume either or both of these in your kit with all the other accessories necessary.
Most mill shops that I'm familiar with would use some form of sheet goods for the shelf. After a template is made and checked it can be used to trace out the shape of the shelf. It may be that the shelf length is to large for a typical 4 X 8 sheet, is so you will have to determine where to joint to create a piece large enough for the purpose and along the way determine where all the other joints will be, taking into consideration strength, grain and finish and what kind of material, method and joinery will be used for the face and soffit of the shelf. The preferred method most commercial mill shops use to join sheet goods edge to edge is glue, biscuits and pocket screws. This is not a piece of furniture that has to resist a lot of dynamic loading. Purists will probably argue for more complicated joinery but it's over kill for this purpose as long as the joints are supported during installation. Nailing or using "finish screws" is OK as long as you are a decent finisher. Red Oak offers lots of opportunities because of the grain and color to hide nails with colored putty after staining or sealing. After roughing out the shape you must decide whether to use the template you created and "template route" to finished dimension or mill the piece to final dimension with a combination power and hand tools. Since retirement I have lots' of time and am tired of listening to the wine of routers and shappers so I would tackle this with rasps, planes, and hand and power sanders. There are a ton of articles in this magazine but when it come to hand tool fabrication there is no one better than Paul Sellars for techniques and simple tools that you could build this project with. You can find him on YouTube and at his web site.
The fascia/soffit construction of the shelf depends on it's thickness. Again you need to create a sketch to visualize it's proportions. You can laminate a finished thin veneer, glue up a curved solid piece of lumber. Veneer is the easiest although it could be prone to de-lamination and is a more easily damaged surface.
If all this sounds hinky the other material you can use is solid lumber. It could be possible to find a piece wide enough, but edge gluing to create the needed width is s.o.p. so I wouldn't hesitate to use lumber in this case. There will be a lot of left overs for other projects so the economics aren't to bad. The biggest consideration is milling straight, flat and parallel rough stock. Again there are a ton of articles in the magazine and every where else to review the tools and techniques needed.
The beauty of using lumber is it can be worked with simple tools, it has fewer fabrication steps and it will look so much more authentic, IMO. The template that you have to create can be used either way.
I'm probably going to deeply into fabrication at this point so first things first; a sketch, then a little more sketch development with a section or two, then a template and finally material selection. Actually that last two are interchangeable it kind of depends on you work methods.
Include in the sketch the crown molding and any underpinning necessary so that it's a realistic view of the final construction.
Good luck and if you get that sketch completed post it here and there will be all kinds of advise you will be able to mull over.
PS I've included a simple SketchUp view of a mantel from a past project although it doesn't have any dimensions or curves. But creating it is always my starting point. So get out your pencil and paper or fire up you sketching program and get your design out of you head and on paper.
Good luck.
Yikes. It's a shelf and moulding, not a baroque secretary.
Great advise. I will sketch and create template first. I made the mantle in this picture for a friend and my wife wanted similar for our house. The curve of our fireplace is the challenge.
She wants a mantle added on the mantle? I don't understand. Are you covering the entire brick structure with wood?
Hi I would just cover the shelf and have 8”crown mounding attached to the shelf.
I'm assuming a wooden "shelf" on top of the brick "shelf," with some kind of crown moulding underneath. Is that all that will be covered in wood? Can you show us the moulding you want to use? Narrow and thin bends much more easily than wide and thick.
You don't mention what tools you have at your disposal or your skill level.
I'm assuming you are covering or replacing the existing brick mantel with a wooden one. My quick assessment would be you need build up a layered molding consisting of a number of edge profiled boards that are cut in an arc. You would need to experiment with the router bits, I'm assuming no shaper is available, you would need, but I imagine some combination of edge profile bits and panel raising bits would get the job done.
It may be simpler to simply let the front edge of the mantel remain straight.
Before undertaking this I think I would check with a custom millwork shop to see what they would suggest and the cost for having such a molding made. I'm a neophyte when it comes to CNC machines but it would see that a larger CNC should be able to create something along these lines.
Great ideas Thank you
There are flexible mouldings you can buy online. I doubt any local supplier would have them. I'm not sure if any are stainable, but they are certainly printable.
8 inches wide is REALLY wide moulding. Regular wood mouldings aren't made that wide. They are put on walls and ceilings and built up from several pieces. I suspect that you will have to do the same for this.
Thank you I found a local source for flexible moulding. I am checking it out tomorrow.
I would make a template to find the arc to fit the brick face, as suggested by reader #7015929. Personally, I have used a different, and successful, method on similar shelving projects. Use a roll of 12-inch wide parchment paper and cut it to length, “plus one inch” on each side to extend beyond the length and width of the existing brick base. Place small strips of double-sided tape randomly on the brick surface to hold down the paper. Overkill is not needed with the strips. Do the same thing on the edges of the brick (in your case, on the front and right edge, and about 1/2 inch up on the left and rear wall surfaces). Starting at the front brick edge, attach the paper, allowing 1 inch to protrude over the front and right edge. Carefully move the paper back towards the wall, securing it to the tape strips. Flatten the paper as much as possible when adhering to the surfaces. When you reach the left side and back, crease the paper with your index finger and secure the remaining vertical paper to the tape on the left and rear wall. Use a utility knife to make a vertical cut in the paper where it meets the rear and left wall. This will help to secure the paper without any bulges at the left wall crease. Tighten the paper as much as possible, as trimming will be next. Starting at the left and back wall, use a sharp utility or pen knife to cut the paper, flush with the walls at the creasing. Cut away and discard the extra paper. Do Not trim the paper at the edge overhangs, as the excess will allow placement onto your mantle board protrusion from the brick surface. Separate the paper from the brick, leaving the strips attached to the “paper pattern”. The tape will help to secure the paper to your mantle board. Lay the pattern on the board, trace the rear arc with a pencil and cut the arc with a scroll saw. Cut to fit as, close as possible. Any gaps will be covered with your moulding. More then a one inch protrusion of your mantle board can be adjusted, by using a wider and longer board for the mantle.
As for bending the crown moulding, I would make 1-inch spaced kerfs along the entire rear edge of the crown moulding. Kerfs should be about 3/8 inches deep through the angle cut of the moulding. If possible, the cuts should be made with a table saw to ensure consistent depth. You can also cut two 1-inch strips of 1/2 inch plywood. Sandwich the moulding between each strip and use a back saw to cut the kerfs, just to the plywood surface. This method will ensure consistent cuts. The narrow kerfs will permit flexible bending of the moulding, without any cracks – and the kerfs are hidden, once the moulding is secured to the wall.
Thank you for your advise. Excellent ideas.
Since your mantle is 12 bricks wide and on an arc it should be under 8' wide. The easiest thing to do is use plywood for the shelf...maybe 2 layers to add a beefier look. Adding solid wood to the front edge is simple.
Stretch a string from point to point so you can measure how wide you need to rip the plywood. Include enough overhang to allow for your trim mouldings, then add 2 inches to give yourself a second swing if you mess up. Use heavy craft paper, a razor, & tape to make a template of the wall's arc to transfer to one edge of the ply. If you want you can go from paper to hardboard or mdf before comitting on the plywood. You can the roughcut the ply and use the hardboard as a routing template.
Shim the plywood to level and flat and aim your fasteners at the mortar joints to give the next owner of the house the option to go back.
I would build the crown in layers. Fine Homebuilding is where I would start to learn how.
I’ll look at flexible moulding. I’m learning so much from all of your posts. Thank you
Thank you MJ. I am absorbing a lot of great ideas from your instructions Thank you.
There's a great instagram poster, carpentry_bymar, who has several useful videos on how to create an arc very simply. Scroll through his videos--I think you'll find a few ideas that will help you solve it.
I’ll check out videos. Thank you for the advise.
This forum post is now archived. Commenting has been disabled