Hot-Rod Your Varnish
Fast-drying, wipe-on blend builds quickly for a durable finish.
Synopsis: When it comes to finding the perfect wipe-on finish, there’s nothing like homemade. At least that’s what Roland Johnson discovered when he started searching for his ultimate finish. This fast-drying oil-and-varnish blend is easy to apply by hand, stands up to wear and tear, and is easy to repair or renew. Just follow Johnson’s recipe for great results every time.
We’d all like a finish that can be applied easily by hand, stands up to the rigors of everyday use, and is easy to repair or renew. Several years ago, in my search for this Holy Grail finish, I started sampling varnishes. I rejected polyurethane because it’s hard to repair and worse to remove if a piece needs a total refinish. I narrowed my search to alkyd-based varnishes, eventually choosing Pratt & Lambert’s no. 38 clear. However, I wanted it to have more water resistance and to dry faster, and I wanted to wipe it on.
The Recipe:5 parts Pratt & Lambert No. 38 alkyd varnish 5 parts Pure tung oil for water resistance 2 parts Japan drier to speed drying time 2–3 parts Pure gum spirits turpentine to make wiping easier You can find a local retailer at prattandlambert.com. The other components can be found at hardware stores, paint stores, or home centers. |
So I started tweaking the stock no. 38 and, through trial and error, came up with a brew that fulfilled my needs. I mixed 10 parts Pratt & Lambert No. 38 alkyd varnish and pure tung oil, added 2 to 3 parts pure spirits of gum turpentine, and zapped the mix with 2 parts of Japan drier.
This custom oil-varnish mixture has a number of advantages. It is easily wiped on and off with a paper towel. It can be wet-sanded into the grain to act as a pore filler. The thin coats dry quickly, reducing the opportunity for dust to get trapped in the wet finish. Often I apply finish in an area that is less than white-room clean, so eliminating the worry about dust is a real bonus. This finish is water-resistant and tough enough to hold up to everyday use, it’s easy to repair or replace, it resists yellowing, and it dries hard enough to be rubbed out to a high-gloss sheen if desired. There are a couple of drawbacks, though. It has a short shelf life (a few weeks before it starts to solidify), so mix only the amount you’ll need for the project. More than with other oil-based finishes, cloths used with this mixture must be laid out to dry because the fast catalytic reaction caused by the Japan driers may create enough heat to spontaneously combust if they are left wadded up.
Mix and Apply
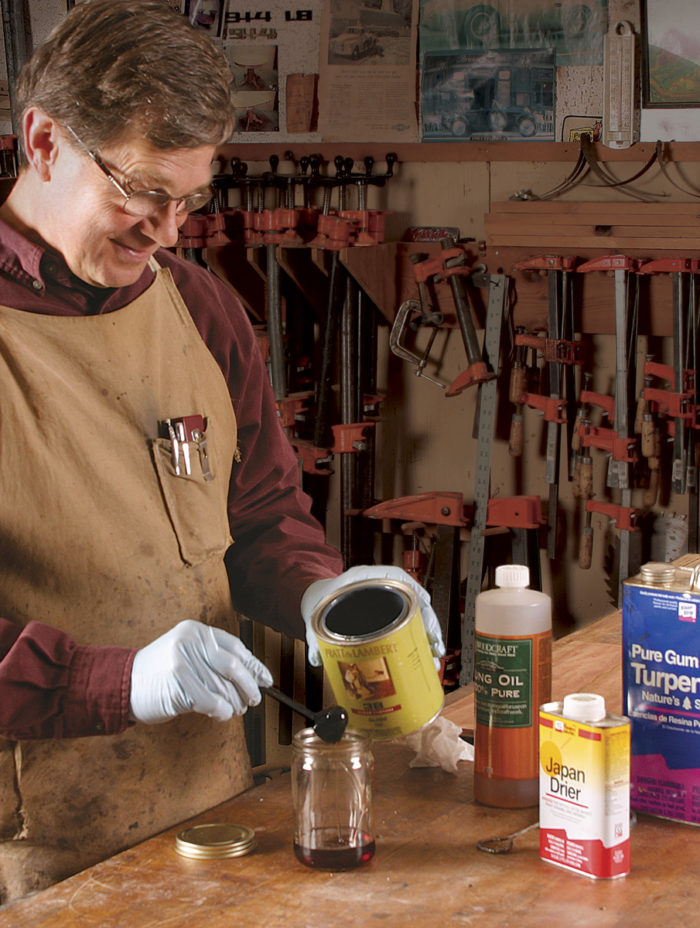
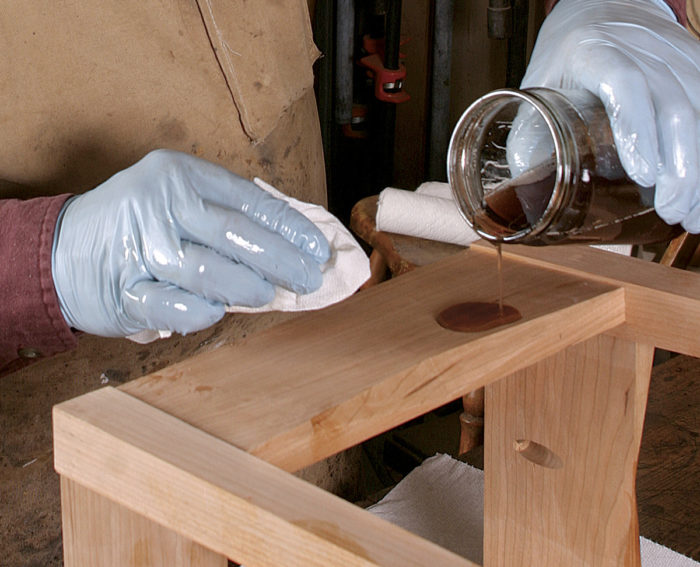
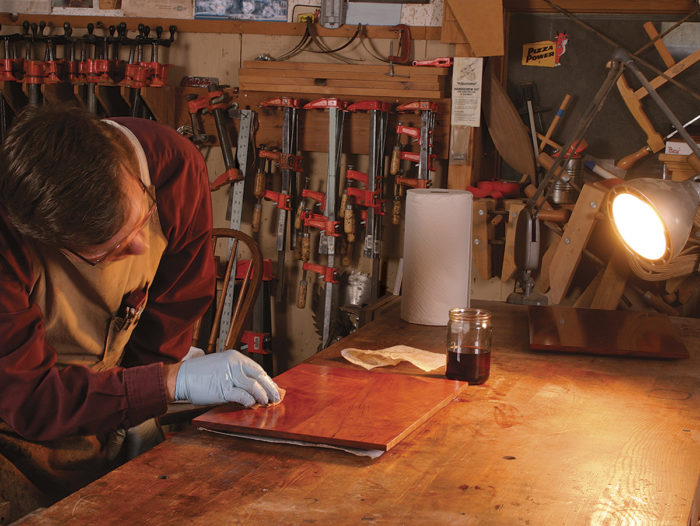
Flood on the first coat
A clear finish looks only as good as the wood beneath it, so good surface preparation is important. I typically sand to P240-grit, then use compressed air or a shop vacuum to clean off the dust, and wipe the surface with a tack rag before applying the first coat.
On horizontal surfaces, pour some finish onto the wood and use a disposable foam or bristle brush or a good-quality paper towel (Bounty works well) to cover the surface with varnish. On vertical areas, apply the finish with the brush. The key to success is an even coating. Keep applying finish until it is no longer absorbed quickly. Areas that absorb the finish will have a dull appearance. A raking light across the surface will help you see the dull spots.
You’ve applied an even film when the sheen across the entire piece is reasonably consistent. At that point, wipe off the excess with a dry paper towel or a lint-free cotton cloth and then allow the finish to dry thoroughly. If the temperature is at least 65°F, 24 hours should be enough time for this first coat.
First coat also can fill the pores
A combination filler and finish—If you want a glossy film finish on open-pored wood, you will need to fill the pores. Spread on the first coat as above, and then sand the surface withP400-grit paper. The resulting slurry will form a paste that fills the pores. Lightly wipe the excess finish off the surface, going across the grain, and allow the finish to dry for 24 hours. To avoid pulling the filler out of the pores, don’t sand the next one or two wiped-on coats.
If you want a glossy film finish on open-grained wood such as walnut, oak, or mahogany, you need to fill the pores. This gives the surface a more attractive, less plastic look.
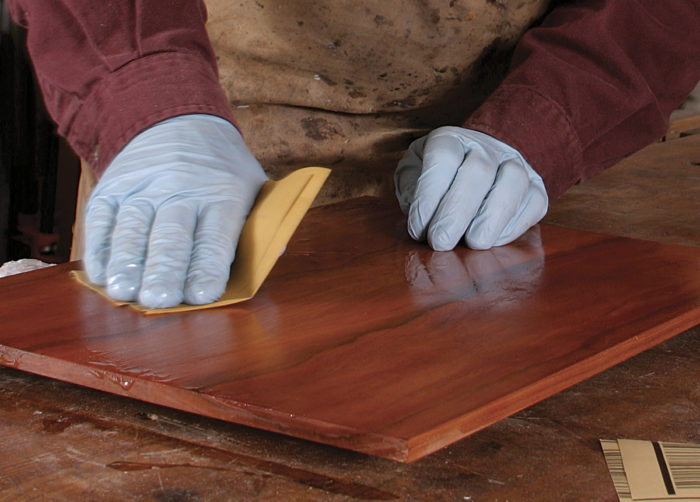
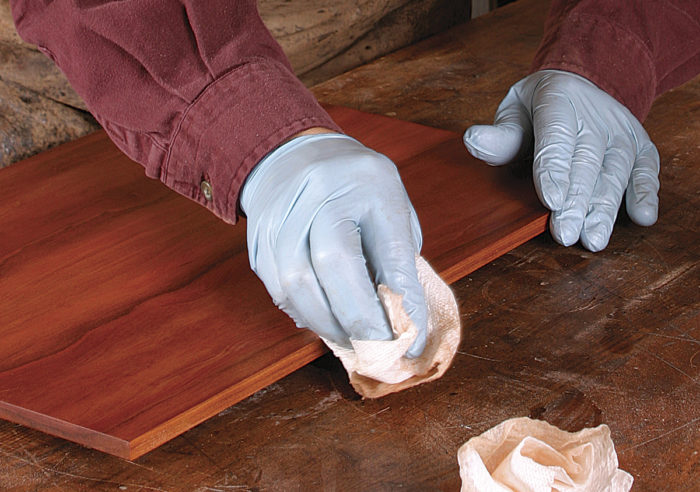
Sand and Build
I sand between each coat of finish with P400-grit paper. The real importance of sanding between coats is to even the surface tension of the next coat of finish. If the surface is left shiny, or with an inconsistent gloss, the wet finish will not flow out evenly.
The varnish is dry enough to sand when the sanding dust is white and doesn’t gum up the paper: “When the swarf is white, the drying is right.” If the dust is brown and forms tiny clumps on the paper, the finish isn’t ready for sanding. Vacuum the dust.
After the first coat, where the wood absorbs a lot of finish and needs longer to dry, successive coats may be applied as quickly as every three or four hours, depending on the temperature and humidity. However, I wouldn’t apply more than three coats in one day as you might trap solvent under the topcoat, resulting in a prolonged curing time. For most surfaces, three or four coats give a nice, even build. For tabletops or other surfaces likely to receive occasional liquid spills, I would apply a minimum of six coats.
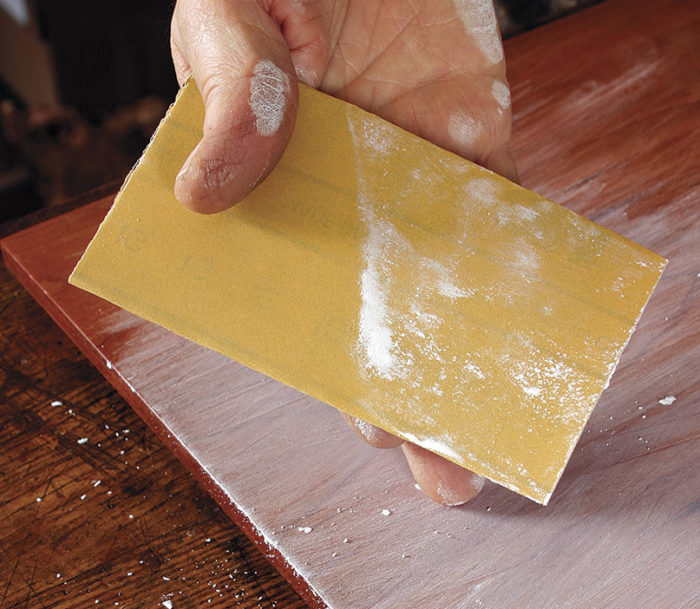
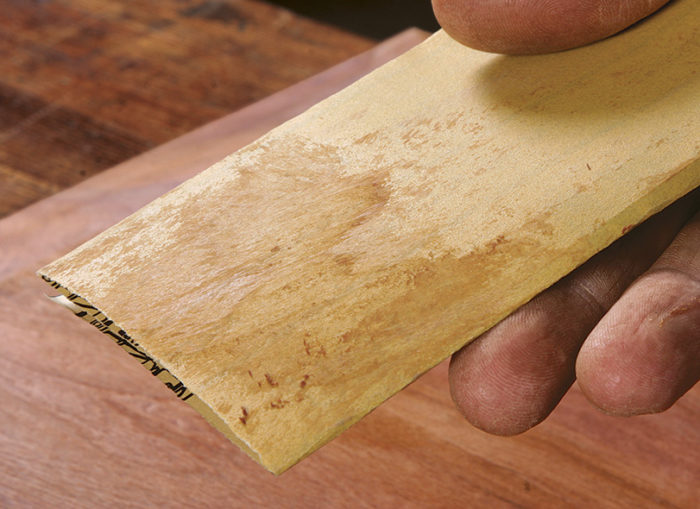
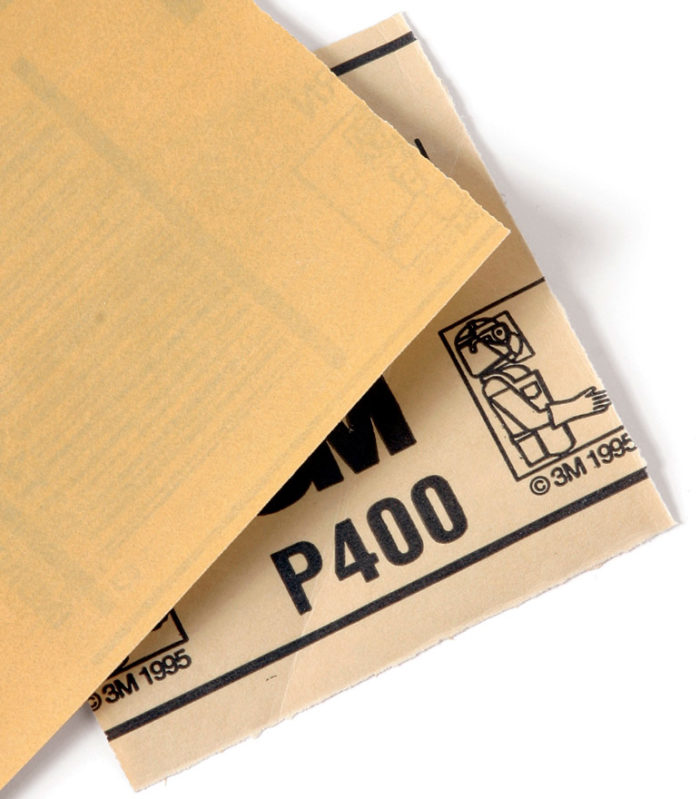
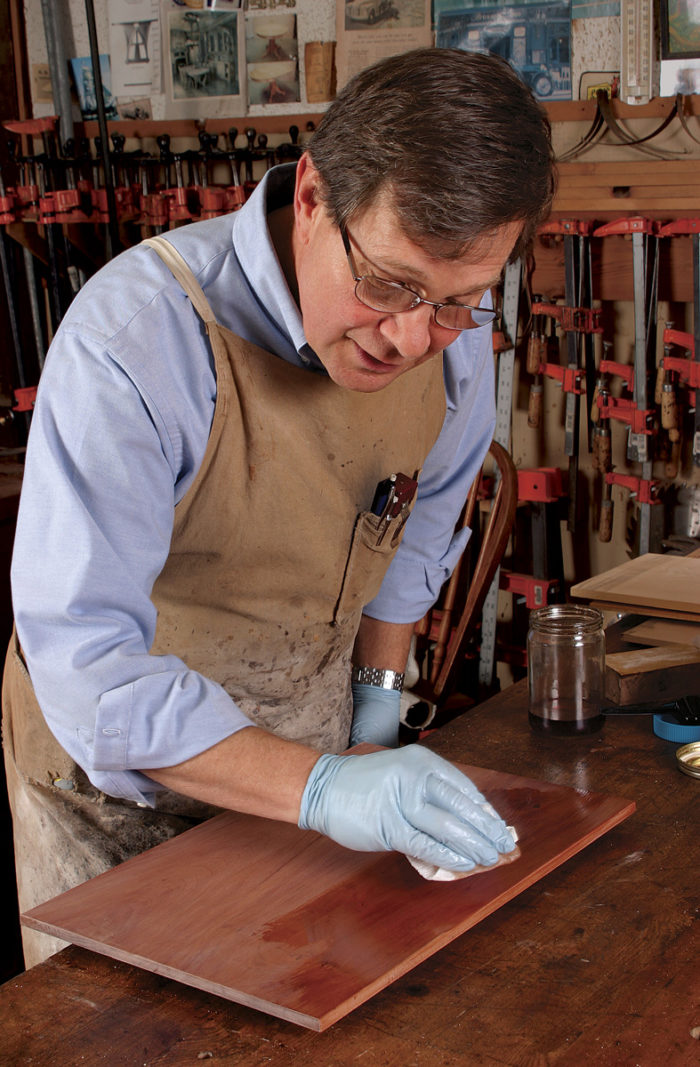
Rub Out and WaxI prefer medium-luster finishes, and to get there I use steel wool and wax. Unfold a pad of 0000 steel wool and lightly rub the surface. Keep checking the surface under a raking light until it shows an even dullness. At that point, vacuum away the steel-wool dust and rub on a thin coat of clear paste wax. Let this dry for 30 minutes and then buff the surface with a clean cotton cloth.
If you prefer a higher gloss, wait several weeks for the varnish to harden, then sand the surface with 600-grit (CAMI) paper, rub it with car polish, and finish with a coat of paste wax. Your piece will now have a finish worthy of your craftsmanship.
Steel wool and wax quickly produce a medium-luster look.
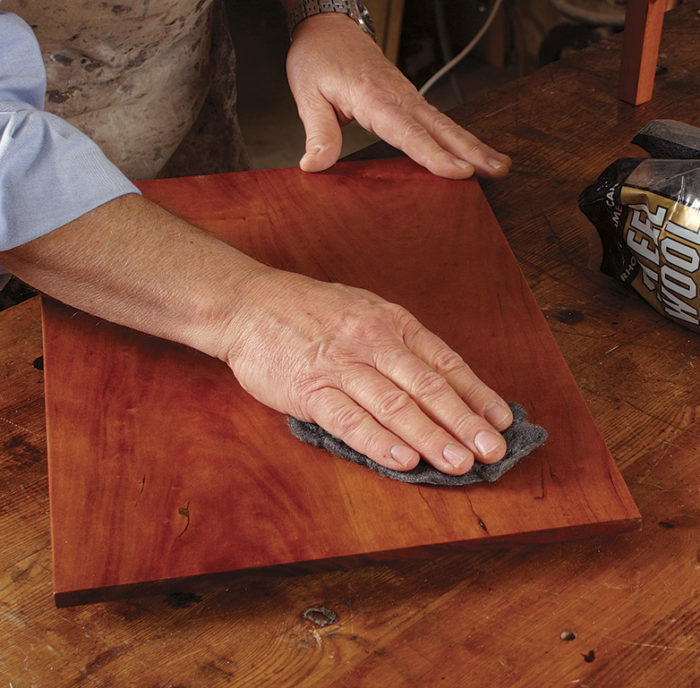
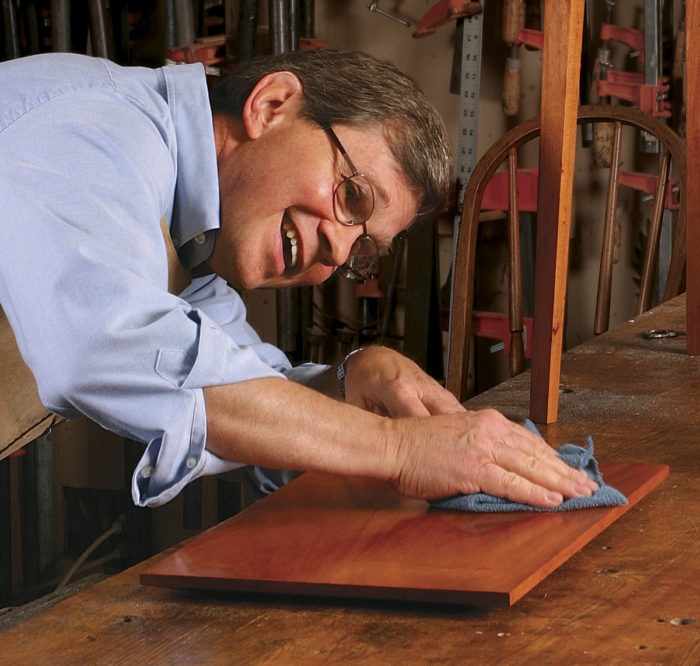
From Fine Woodworking #198
To view the entire article, please click the View PDF button below.
Fine Woodworking Recommended Products
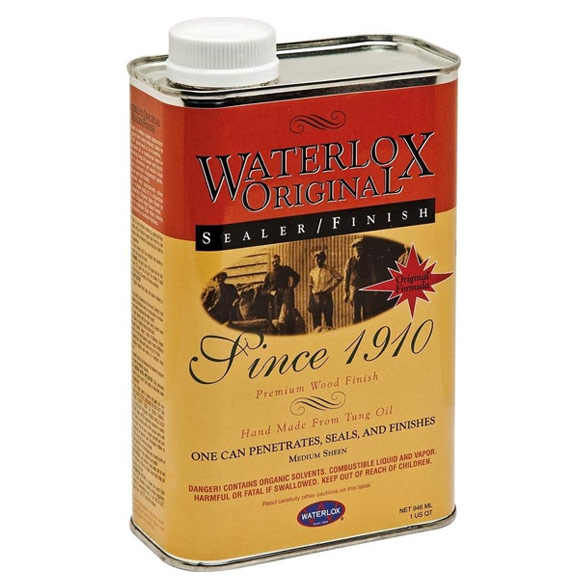
Waterlox Original
Diablo ‘SandNet’ Sanding Discs
Osmo Polyx-Oil
Log in or create an account to post a comment.
Sign up Log in