Sliding Table Saws: Is One Right for You?
These premium machines are loaded with features that add precision and versatility.
Synopsis: Long a fixture in professional cabinet shops where their accuracy, efficiency, and ability to handle large sheet goods is crucial, sliding tablesaws are becoming more and more accessible to smaller shops. With more manufacturers offering entry-level models, it may be time to take a look at these machines and see if one is right for you. Dan Chaffin has been using sliding tablesaws for years, and here he offers a rundown of their advantages and disadvantages, as seen from a pro’s perspective.
Sliding tablesaws have long been a fixture in production cabinet shops, where they’re invaluable because they handle sheet goods so exceedingly well. But sliders aren’t just for sheet goods; they handle solid wood excellently too. On a slider, the workpiece rests on the sliding table and cutting the stock is simply a matter of pushing the sliding table through the cut. There’s no wrestling with the workpiece during the cut regardless of its size or the condition of its edges, and accuracy is not influenced by technique; rather, accuracy is a product of the precision built into the saw. You can also lock the sliding table in place and push boards by hand, if you prefer.
In spite of their versatility, efficiency, precision, and safety, sliding tablesaws have often been considered out of the question for smaller shops because of their high price and large footprint. But with more manufacturers offering them, there are now several entry-level models that can be had for around the cost of a high-end cabinet saw, and sliders are increasingly finding their way into smaller pro shops and some home shops as well.
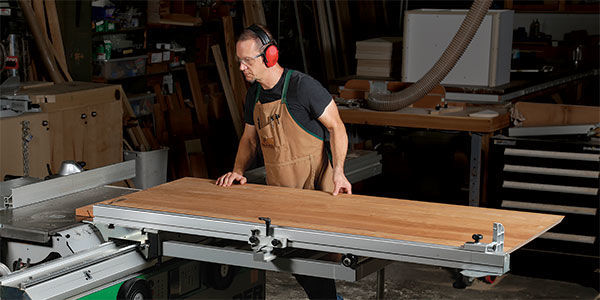
For years, a sliding tablesaw was the heart of my pro shop, and I got pretty familiar with the advantages and disadvantages of this machine. So while I can’t decide if a slider’s right for you, I’ll try to make your choice a little clearer.
Most sliding tablesaws are beautifully built
Although there are exceptions, sliders are typically built to very high standards. They are large, heavy machines, and for their sliding components to work properly, the design and manufacture must be spot on. As a result, these machines tend to deliver incredible precision, smooth action, and dependable repeatability. Heavy, durable fences and stops ensure that settings and adjustments do not drift over time.
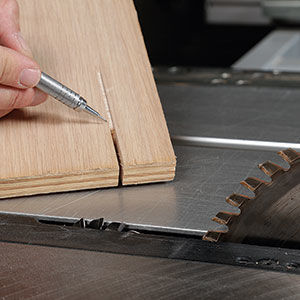
There’s also a staggering list of options available with some sliding saws, allowing you to customize the machine to your space and intended use. One example is a scoring blade, a tiny blade spinning ahead of the main blade to lightly score the underside of the panel, helping eliminate tearout, particularly on plywood. Some manufacturers offer the option of combining multiple machines— jointer, planer, shaper, saw—into one cabinet, somewhat offsetting the slider’s enormous footprint.
Other options include digital scales, alternate locations for on/off switches, motorized adjustments, crosscut fence length, sliding table length, motor size, and even the size of the arbor. You’ll pay for these, but they can customize the tool to a specific shop and user.
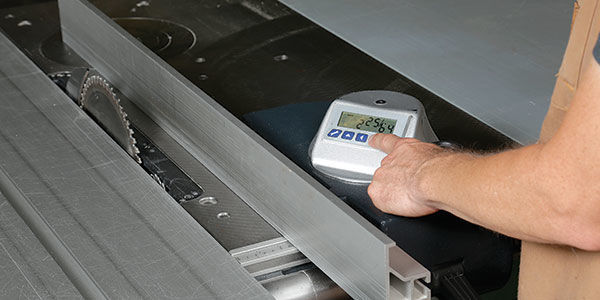
Efficiency and ease of use
This high quality of machining directly translates to a machine that’s efficient and, for many tasks, a breeze to use.
Big boards are a small concern
Take, for instance, sheet goods, which can be a handful on a cabinet saw. Imagine cutting a 4×8 sheet down to 4×7 on a cabinet saw; it would be difficult if not dangerous. With sliders, all you do is put the sheet in place and push. The sliding table guides the work past the blade in a perfectly straight path. The slider is also great for cleaning up unreliable factory edges, even the long ones, before breaking down the rest of a sheet.
Cutting a long edge straight with the sliding table is called a straight-line rip, and it works just as well for lumber with waney edges as it does for plywood, greatly speeding up milling. How many passes—not to mention how much effort—does it take to straighten the edge of an 8-ft. board on your jointer? With a slider, your only limit is the length of the sliding table’s stroke.
On the fences
A slider has two fences, a rip fence and a crosscut fence. The rip fence is the same as on a cabinet saw, but with a couple of perks that you may not find on that machine. For one, on many sliding tablesaws you can slide the rip fence toward you, ahead of the blade, and use it as a crosscut stop. The fence can also be flipped facedown, making its top edge the bearing edge. This is helpful because the top is much narrower than the face, allowing you to use a push stick close to the fence when ripping thin stock without jamming your knuckles.
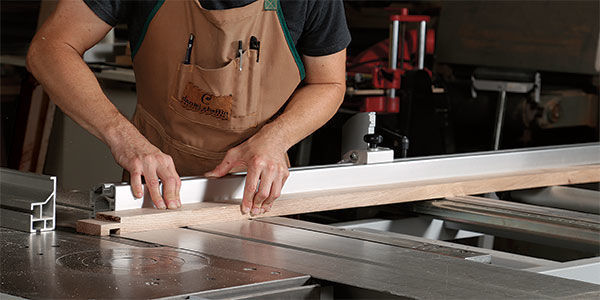
Because the crosscut fence attaches to the sliding table, it benefits from that mechanism’s accuracy and smoothness, making crosscuts snap-on pieces large and small, whether the fence is set to make a 90° crosscut or a mitered one.
Design contributes to a safer use
In terms of safety, sliding tablesaws have a number of advantages over ordinary tablesaws. For rips using the sliding table, the risk of kickback is smaller compared to just pushing the board by hand. And whenever the sliding table is being used for a cut, the saw’s design encourages the user to be in a safe position well to the left of the sawblade.
Additionally, I’ve been thankful for the automatic blade brake on sliders a number of times. The brake ensures that when the machine is switched off, the blade quickly stops. This significantly reduces the chance of the user coming in contact with a spinning blade when reaching for a freshly cut workpiece.
Sliding tablesaws also come equipped with riving knives (which are also standard issue on the newer cabinet saws), an important safety feature that helps eliminate dangerous kickback.
Some caveats before you buy
Buying such a high-tech saw is a big investment, not just in money but in space, too. While entry-level models are a little over $3,000, comparable in price to high-end cabinet saws, that gulf can quickly widen with higher-end sliders, some of which cost north of $20,000.
Space is a consideration, too. Sliding saws have an enormous footprint. Including the stroke of the sliding table, they can take up about four times more space than a cabinet saw with both a standard outfeed and side-feed support. Plus, if you get a slider with a long enough stroke to rip a full sheet of plywood, you will spend a fair amount of your shop time walking around the table to get to your perfectly dimensioned boards.
Although a slider’s size, mass, and sliding capacity are ideal for big parts, some folks may find it a bit difficult to use for small parts. While a cabinet saw fitted with a shopmade crosscut sled will handle a stack of small pieces with grace and efficiency, the slider when faced with the same task is precise but not terribly nimble. A well-made sliding table can be quite heavy, and despite the ultrasmooth sliding action, there’s a lot of inertia. And you have to pull the table back to you after each cut.
If you decide that a slider will fit in your shop and your budget, there are still a few other issues to consider. Moving such a saw is a major operation requiring a battle plan and special equipment. While cabinet saws are heavy, sliding saws are on a completely different scale. The one in this shop weighs over a ton and to move it in we had to use a combination of an engine hoist, ramps, and some extensive dismantling. Smaller models can come in around 700 lb. For a cabinet saw, if you want to move it often, you just invest in a mobile base—not always an option with a slider. Initial setup and calibration of a slider can also be quite involved. They’re complex machines that need to be set up for precision. Also, the instructions for many sliders are translated into English and can sometimes be unclear. And last, while sliding tablesaws are very easy to use once you’re familiar with them, there is a learning curve.
Does it fit your work?
So let’s say you can afford a slider, get it into your shop, and still have room to move. It’s also important to consider the type of work you do. If you work with large boards and sheet goods and often work with production in mind, a sliding tablesaw could very well improve your workflow. It did for me. When I was producing built-ins and other large, standalone pieces, my slider was integral to the way I worked wood. So if you ever mull over buying one, don’t just consider whether it will fit into your budget or shop; also think about whether it will fit the way you work.
From Fine Woodworking #272
For the full article, download the PDF below:
More on FineWoodworking.com:
- Dream Machines: Kevin Rodel’s Ulmia 1710 sliding tablesaw
- Large-Capacity Sliding Tables
- Shopmade Sliding Crosscut Table
Fine Woodworking Recommended Products
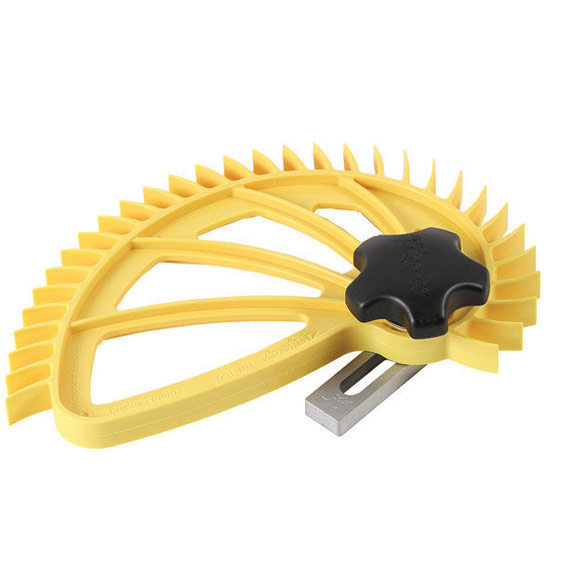
Hedgehog featherboards
Ridgid R4331 Planer
Comments
This article fails to explain how much space to place around the tool! Can it be against a wall on the non-sliding table side?? Also, why doesn't it provide some examples of low, medium and high price points and the trade offs!!
Also it fails to mention that many European machines can incorporate a tilting spindle shaper, which also makes use of the same slide table capabilities. (This appears to be the kind of machine the author is using).
I have had a sliding table saw for 15 years. It is a beast. At 1,200 pounds it does not move around the shop much. I find it is nimble to use if you work with it. Then I can cross cut a 4 x 8 sheet easily. But, I also have a second 4 foot wide table saw on a mobile heavy metal base I fabricated to be the same height has the slider. I can roll it around the slider easy to act as an out feed table. It is so nice to have 2 table saws set up while on a project. Lessens the blade changes and set ups. A lot of time one is for ripping, and the other cross cut or dado setup. But then I have 2 bandsaws and 2 lathes. Yea I am a nut.
I would tell others to really make sure they have the room and the saw works for them. For example on the slider the rip fence only works on the right side of the table. But then I have my 2nd table saw that does.
Log in or create an account to post a comment.
Sign up Log in