A Fine Shop in a Renovated Garage
Thoughtful renovation and a savvy layout make this shop exceptional.
When my wife, Jen, and I moved to Pittsburgh in 2011, the property we purchased had several outbuildings, one of them a somewhat forlorn two-car garage. Despite its aesthetic shortcomings, the building was structurally sound and well situated, and it made sense that it would become my workshop.
Over the next year and a half, I did a gut renovation, stripping the building to its studs, moving and resizing window and door openings, and replacing everything from sheathing to drywall. I was careful in all my choices, because I wanted the shop to be reflective of the work that would be produced inside: functional, understated, subtly embellished, and meticulously crafted with lovely materials. Drawing on my experience working in other shops, and on some research, I aimed to create a space that would be comfortable through Pittsburgh’s muggy summers and frigid winters, have plentiful natural and artificial light, and make the most of the building’s 20-by-24-ft. footprint.
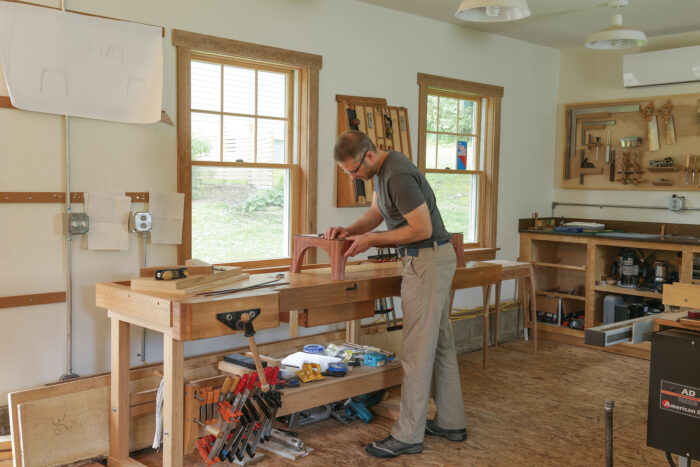
Working from the outside in
Since the building is fairly small and I was putting a lot of work into the renovation, it seemed justifiable to choose very nice materials. For the siding I used true quartersawn spruce clapboards sawn by Ward Clapboard Mill in Vermont. For the exterior trim I opted for MiraTEC, a pre-primed MDF product designed for exterior applications. I sheathed the soffits with clear, vertical-grain Douglas fir porch flooring, and I built the gable brackets of Douglas fir as well, but with a cabinetmaker’s flourish: faceted sapele plugs over the screws. I built the entry door of Douglas fir also, and used sapele for the jambs and sill.
After some deep research, I decided to heat and cool the shop with a Fujitsu ductless mini-split heat pump (see “Heating and Cooling Your Shop,” pp. 53–57), which has turned out to be a great decision. With this type of system it really pays to insulate well, and after I hired an electrician to upgrade the electrical service and brought in a drywaller, I had an insulation contractor blow cellulose into the walls and above the ceiling. To provide further insulation, as well as air sealing, I installed sheets of 3⁄4-in.-thick polyisocyanurate rigid foam insulation over the existing siding, foaming all the joints and all around the perimeter. Over that layer went a layer of housewrap, followed by 1×3 vertical strapping as nailers for the spruce clapboards.
To insulate the concrete floor slab, I laid down 4×8 sheets of 1-in. extruded polystyrene (XPS) rigid foam with tongue-and-groove edges, and over them I laid a floor of 3⁄4-in. tongue-and-groove oriented-strand board (OSB). I screwed the OSB to the slab with Tapcon screws, just a few screws per sheet.
Consider the layout
With the renovation nearly complete, I began to think about the layout of the space. I knew I wanted my bench to be on the south wall, which would receive the best natural light and provide a view toward the house. I located the jointer on the opposite wall, roughly centered so the direction of feed is parallel to the long axis of the shop. On the other two walls I built long counters, one for benchtop machines, the other for a sharpening station. I put my cyclone dust collector in the far corner of the shop and I placed the lathe, which I use infrequently, behind the swing of the entry door.
That left the center of the space, where I clustered my tablesaw, planer, and outfeed/assembly table. This arrangement made for less dust-collection ducting and less electrical work, and it enabled me to use one outfeed surface for both machines. It also allowed me to keep a substantial area open on one end of the shop where pieces that are in progress can stand clear of traffic and kickback.
Hanging the hand tools
I love machines—and I’ve been gradually upgrading mine to heavy-duty vintage American models—but hand tools are just as pivotal in my work, and storage for them was a key consideration as I fitted out the shop. I built a wall-hung till to hold my handplanes, with extra room in case (!) I purchase more in the future, and mounted it to the wall adjacent to my bench. Most of the rest of my hand tools are organized on a piece of solid-edged plywood mounted with French cleats to the wall above my sharpening station. I made a variety of holders for the different tools, and attached them with screws driven through the back of the plywood so no fasteners are visible.
A smart layout
Korsak’s shop layout provides efficient dust collection, best use of daylight, and an open space for assembly.
Mike Korsak builds custom furniture in Pittsburgh, Pa.
For the full article, download the PDF below:
Comments
Mike, if you are interested, I have a friend with a three phase drum sander - very large that he would like to sell. I think he probably would sell it at a very reasonable price and could get the details if you are interested. he inherited it from an uncle and has never used it. Located near Warren Ohio and would be an easy drive from Pittsburgh. Let me know curtismoll@gmail.com
Wow, what a dream shop! I wondered if your heavy tools would settle and create dips in the foam/OSB floor? In one photo I can see what appears to be a separate base under the joiner. Can you describe this?
Log in or create an account to post a comment.
Sign up Log in