Designer’s Notebook: Artistry, technology, and craft
Former industrial designer Gerard Furbershaw now creates art furniture, which he describes as "art you can sit on." He fashions most of his pieces out of 13-ply maple plywood, using positive/negative space to make forms that are about half plywood and half empty space.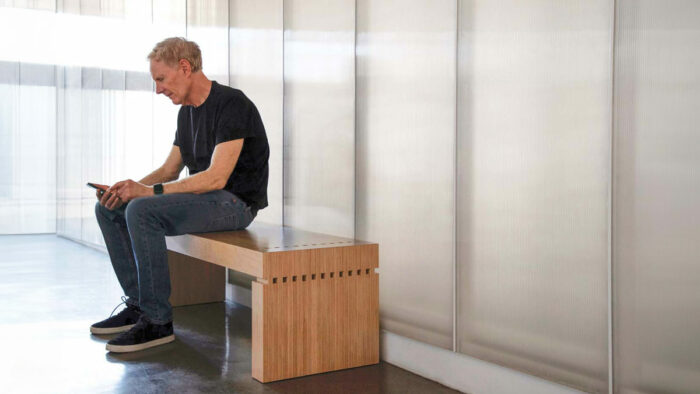
Synopsis: Former industrial designer Gerard Furbershaw now creates art furniture, which he describes as “art you can sit on.” He fashions most of his pieces out of 13-ply maple plywood, using positive/negative space to make forms that are about half plywood and half empty space.
In my previous career as an industrial designer, I worked on a number of conceptual furniture projects and became captivated with the notion of furniture as art. I launched Furbershaworks to pursue work in the art furniture domain, the creation of art you can sit on. I transformed from an industrial designer who used my design skills to solve clients’ business problems to an artist focused on self-expression.
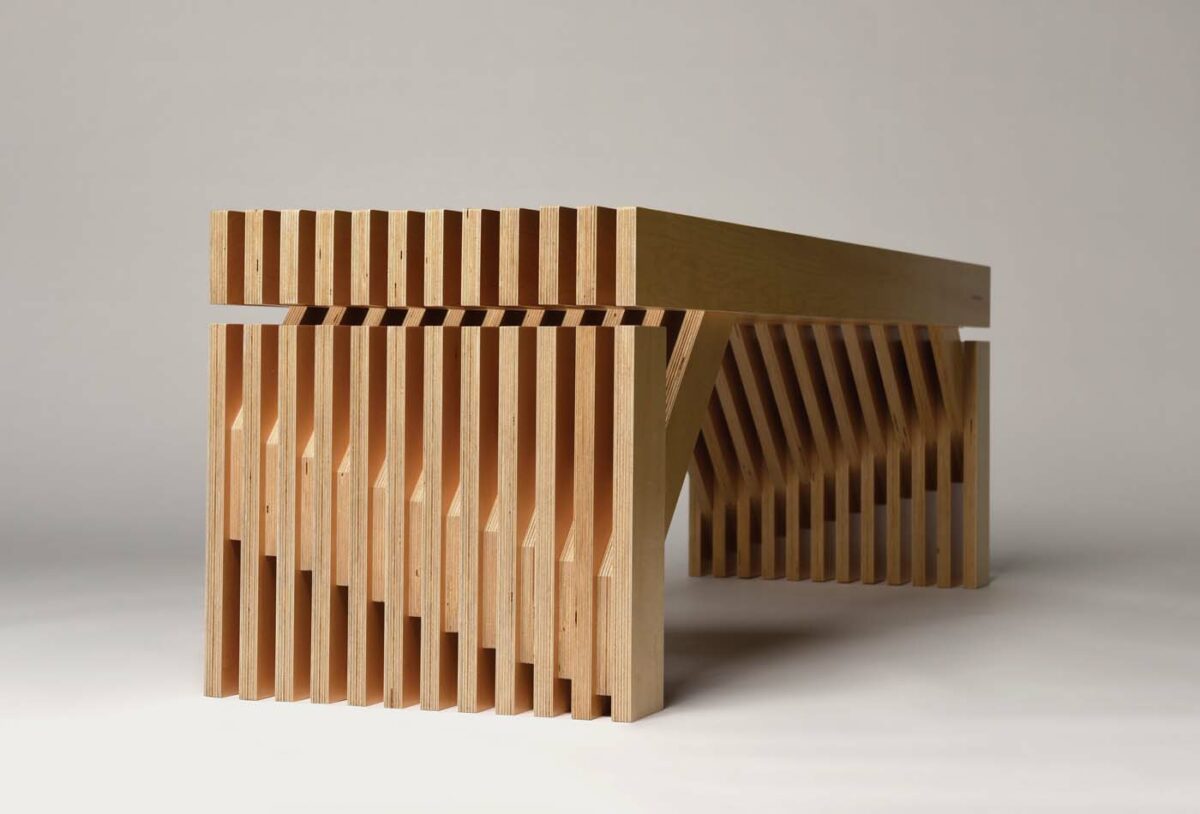
The three key pillars: layering, contrast, and negative space
Initially my focus at Furbershaworks was exploring the possibilities of art furniture enabled by 3D printing. I began looking at pieces that were composed of layered plywood parts that I could make myself. I became fascinated with using positive/negative space to create forms that appeared solid visually but were in fact about half plywood and half empty space. I also liked the effect created by contrasting the plywood’s face and edge grain. My go-to material has been 13-ply maple plywood, but recently I have begun making pieces from Plyboo bamboo plywood.
Industrial design skills still come in handy
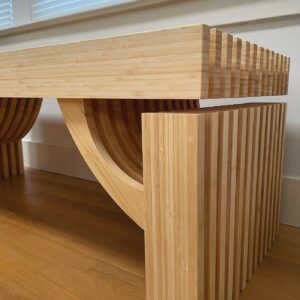
Even though I now see myself as an artist, I continue to rely heavily on my industrial design skills to design and make my pieces. All of my work is created in Rhino, a computer-aided design (CAD) surface modeling software. After I’m finished creating the Rhino model, I export it into KeyShot (a rendering software). The images generated by KeyShot enable me to visualize the piece more vividly and to make refinements. I have also used the Rhino CAD files to have laser-cut maple plywood scale models made. Using 3mm plywood at 1/6 scale means that the proportions are aligned accurately with the full-scale piece’s 18mm plywood. I also use the CAD files to have the full-size parts for my pieces machined using computer numerical control (CNC).
The craftsmanship of finishing
After the parts are CNC machined, I sand, apply finish, and assemble them into the final piece. This part of the process relies on old-fashioned craftsmanship, introducing an element of tender loving care.
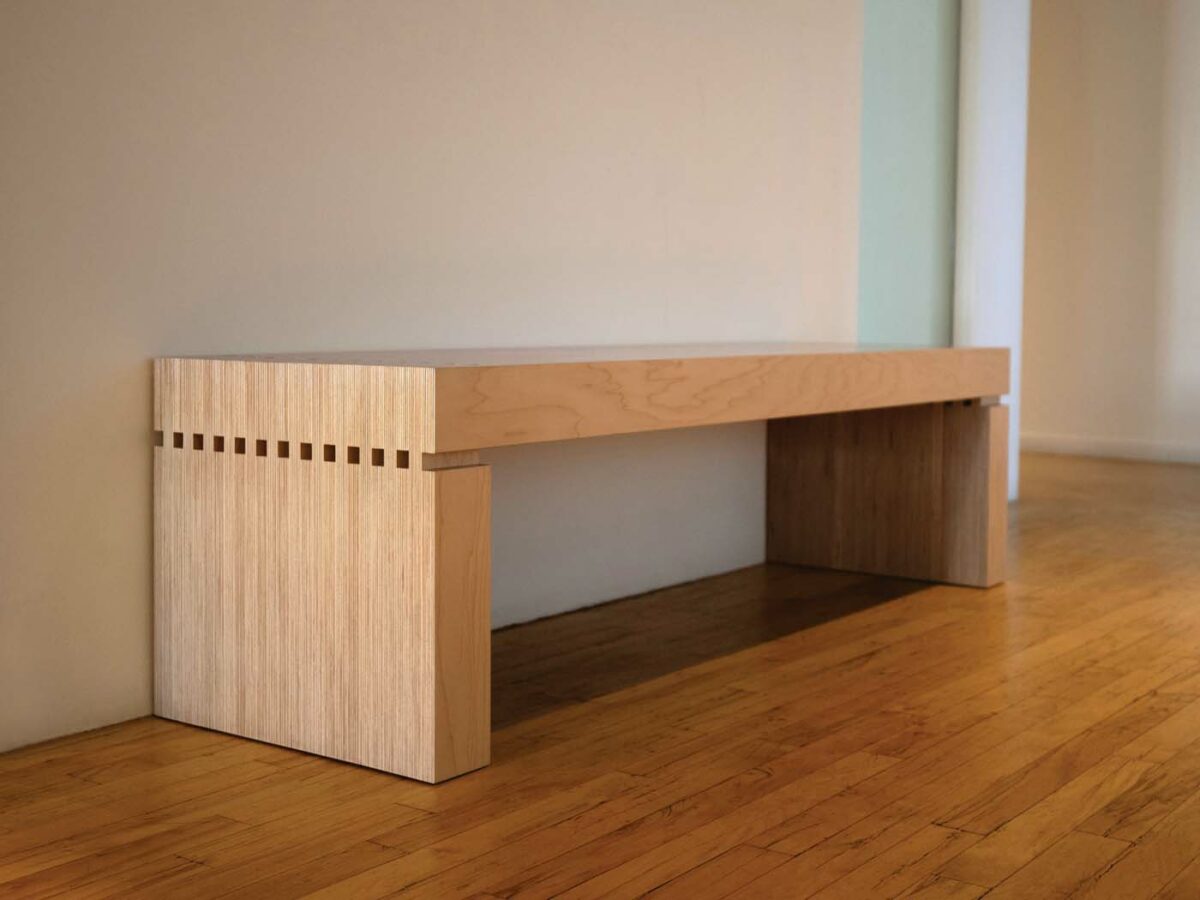
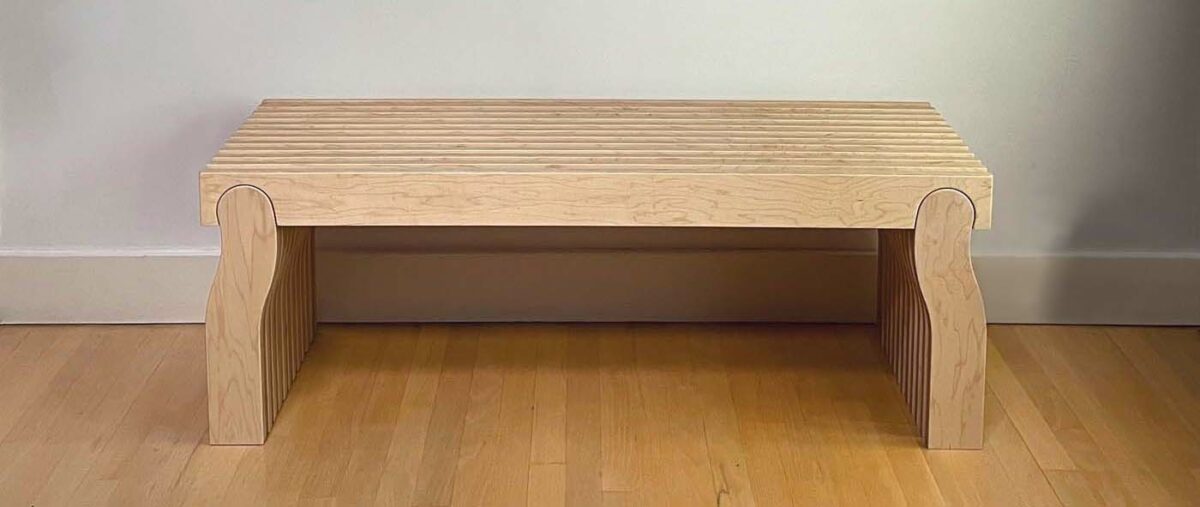
I have been using Osmo Polyx-Oil or Osmo Polyx-Oil Raw (which keeps yellowing to a minimum) as a finish. I like Osmo because it’s durable, the wood’s surface can be easily refinished if it’s scratched, and it’s VOC free. Its natural oil and wax coating is the crowning ingredient in my process.
The Furbershaworks legacy
Like most artists, I would like to leave a legacy. My pieces are made to last so future generations can experience them. Artists sign their paintings. I literally brand my work with the Furbershaworks name to lay the groundwork for that legacy.
-Gerard Furbershaw makes his pieces in Menlo Park, Calif. His website is furbershaworks.com.
Log in or create an account to post a comment.
Sign up Log in