All About Sharpening
The tremendous variety of cutting tools found in a woodworking shop has helped to create a similar variety of sharpening systems. They range from the plain to the exotic, and almost always rely on some kind of abrasive material.
What Counts:
• Type of abrasive
• Speed of material removal
• Durability of sharpening surface
• Flatness of sharpening surface
• Fineness of abrasive particle.
Most abrasives used in sharpening are man-made materials. This broad category includes synthetic oil stones made from aluminum oxide, silicon carbide, ceramic waterstones and diamond paste. The exceptions are Arkansas stones, available in different levels of hardness, and quarried stones from Japan.
The stone approach
Sharpening stones are the most common form for abrasives. Arkansas stones and some man-made materials are lubricated with light oil or kerosene, which helps float away debris and prevent the pores of the stone from clogging. But oil can be messy, a disadvantage that has steered many woodworkers to waterstones. They are kept in a water bath when not in use, or misted with water just before use. Waterstones cut faster than oilstones but they also wear more quickly and must be flattened regularly. Ceramic stones are another option, cutting faster than oilstones but not as quickly as waterstones. They’re also harder to flatten.
Using natural materials
The grading system for naturally quarried stone is less precise than the scale used for waterstones. Arkansas stones range from Washita, the coarsest grade, to hard black, which produces a finer edge. By contrast, waterstones are graded by grit, like sandpaper. Coarse stones of 220 grit remove material quickly but produce a fairly rough edge while a very fine 8000-grit stone produces a mirror polish. Common grits also include 800, 1000, 1200, 4000, 5000 and 6000. Combination stones have one grit size on one face and another on the opposite face.
The sandpaper approach
Wet/dry silicon carbide sandpaper also is used to sharpen edge tools. It’s usually placed on a piece of plate glass or other flat surface when sharpening straight edges on chisels or plane blades, but it also can be wrapped around a pipe or dowel for sharpening curved edges.
Diamonds are forever
Synthetic diamonds are used in a variety of sharpening systems, including stones, flat and curved files and in a paste that can be used on a hard block of wood, glass or leather. Diamond stones wear very slowly and they are hard enough to hone carbide cutting edges (conventional oilstones and waterstones are not). But even the finest diamond stone leaves a rougher edge than a fine waterstone, and they are impossible to flatten should they become hollowed. Diamond paste, on the other hand, produces an extremely fine edge and can be used after oil- or waterstones for a final honing.
Grinders for sharpening
Grinding wheels for electric bench grinders are made with different types of abrasive particles and a binder. Stones with a hard binder don’t wear out quickly, but they can produce more heat. Soften bonds allow new abrasive particles to be exposed during use, but they wear more quickly.
Jigs ensure accuracy
With practice, sharpening an edge tool on a stone by hand will produce a straight, even bevel. But there are a variety of manufactured jigs that make the process a little easier and ensure consistent results. Many rely on some kind of roller that follows the stone and a clamp that prevents the blade from moving; a few can be used on both a grinder and sharpening stone. There also are specialized jigs for curved tools, twist drills and jointer/planer knives.
Fine Woodworking Recommended Products
Veritas Wheel Marking Gauge
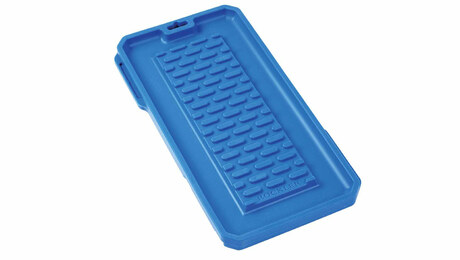
Rockler Silicone Sharpening Stone Tray
Suizan Japanese Pull Saw
Log in or create an account to post a comment.
Sign up Log in